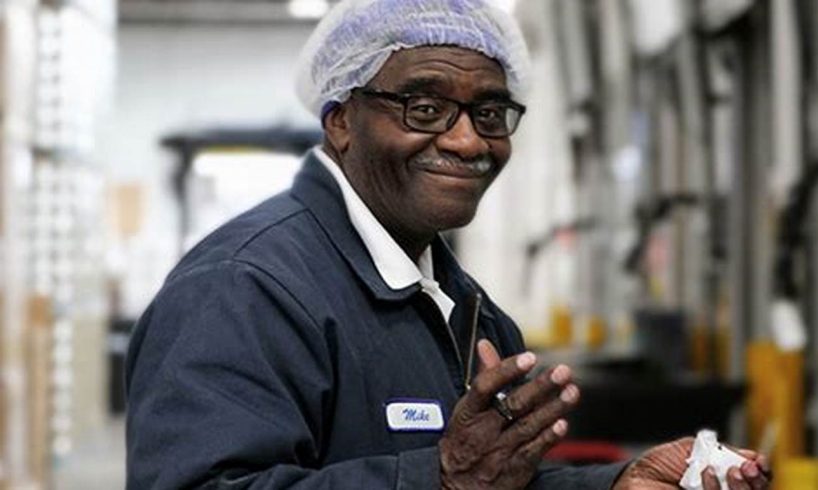
Lawrence Foods Inc., a leading provider of food and beverage distribution services, operates a state-of-the-art logistics center in the heart of the Midwest. This facility plays a crucial role in the company’s operations, serving as a central hub for the efficient storage, handling, and distribution of a wide range of food and beverage products.
The Lawrence Foods Inc. logistics center is strategically located to optimize transportation routes and minimize delivery times to customers throughout the region. The facility is equipped with cutting-edge technology, including automated systems and advanced inventory management software, which enable efficient and accurate order processing and fulfillment. The center also adheres to the highest standards of food safety and quality control, ensuring that products are stored and handled in optimal conditions.
The logistics center is a vital asset to Lawrence Foods Inc., enabling the company to meet the growing demands of its customers and maintain its position as a leading provider of food and beverage distribution services.
1. Strategic location
The strategic location of Lawrence Foods Inc.’s logistics center is a key factor in the company’s success. The facility is located in the heart of the Midwest, which provides easy access to major transportation routes and allows the company to quickly and efficiently distribute its products to customers throughout the region.
- Proximity to customers
The logistics center’s proximity to customers minimizes delivery times and reduces shipping costs. This is especially important for perishable food and beverage products, which need to be delivered quickly to maintain their freshness and quality.
- Access to transportation hubs
The logistics center is located near major highways, railroads, and airports, which provides Lawrence Foods Inc. with multiple options for transporting its products. This flexibility allows the company to choose the most efficient and cost-effective shipping methods for each customer.
- Central location within the Midwest
The Midwest is a major food and beverage production region, and Lawrence Foods Inc.’s logistics center is centrally located within this region. This gives the company access to a wide range of suppliers and allows it to quickly and easily source the products that its customers need.
- Availability of skilled labor
The Midwest has a large pool of skilled labor with experience in the food and beverage industry. This ensures that Lawrence Foods Inc. has access to the workers it needs to operate its logistics center efficiently and effectively.
Overall, the strategic location of Lawrence Foods Inc.’s logistics center provides the company with a number of competitive advantages. The proximity to customers, access to transportation hubs, central location within the Midwest, and availability of skilled labor all contribute to the company’s ability to efficiently and cost-effectively distribute its products to customers throughout the region.
2. Advanced technology
Lawrence Foods Inc.’s logistics center is equipped with advanced technology that enables the company to efficiently and accurately store, handle, and distribute its products. This technology includes:
- Automated systems
The logistics center uses automated systems to streamline a variety of tasks, including inventory management, order processing, and product handling. These systems improve efficiency and accuracy, and they help to reduce labor costs.
- Advanced inventory management software
The logistics center uses advanced inventory management software to track the movement of products through the facility. This software provides real-time visibility into inventory levels, and it helps to ensure that products are always available to meet customer demand.
- Radio frequency identification (RFID) technology
The logistics center uses RFID technology to track the movement of products and equipment. This technology helps to improve inventory accuracy and it can also be used to track the location of products in real time.
- Voice-directed picking
The logistics center uses voice-directed picking technology to improve the efficiency of order picking. This technology allows workers to pick orders using voice commands, which frees up their hands and eyes to focus on the task at hand.
The use of advanced technology in the logistics center has a number of benefits for Lawrence Foods Inc., including:
- Increased efficiency
The automated systems and advanced inventory management software help to improve the efficiency of the logistics center. This allows the company to process orders more quickly and accurately, and it helps to reduce labor costs.
- Improved accuracy
The advanced technology helps to improve the accuracy of the logistics center. The automated systems and advanced inventory management software help to reduce errors, and the RFID technology helps to ensure that products are always available to meet customer demand.
- Reduced labor costs
The automated systems and advanced technology help to reduce labor costs in the logistics center. This allows the company to save money on labor costs, and it frees up workers to focus on other tasks.
Overall, the use of advanced technology in the logistics center has a number of benefits for Lawrence Foods Inc. This technology helps to improve efficiency, accuracy, and labor costs, and it helps the company to better meet the needs of its customers.
3. Efficient operations
Efficient operations are essential for any logistics center, and Lawrence Foods Inc.’s logistics center is no exception. The center’s efficient operations are due to a number of factors, including:
- Well-trained staff
The logistics center’s staff is well-trained and experienced in all aspects of logistics operations. This includes training in the use of the center’s advanced technology, as well as training in best practices for inventory management, order processing, and product handling.
- Optimized processes
The logistics center’s processes are constantly being optimized to improve efficiency. This includes using data analytics to identify areas for improvement, as well as implementing new technologies and best practices.
- Collaboration with suppliers and customers
The logistics center collaborates closely with its suppliers and customers to ensure that products are delivered on time and in full. This includes working with suppliers to ensure that products are available when needed, and working with customers to understand their needs and expectations.
- Continuous improvement
The logistics center is committed to continuous improvement. This includes regularly reviewing its operations and identifying areas for improvement. The center also invests in new technology and training to ensure that it is always using the most efficient methods.
The efficient operations of Lawrence Foods Inc.’s logistics center have a number of benefits, including:
- Reduced costs
The efficient operations of the logistics center help to reduce costs for Lawrence Foods Inc. This is due to the reduced labor costs, the reduced inventory carrying costs, and the reduced shipping costs.
- Improved customer satisfaction
The efficient operations of the logistics center help to improve customer satisfaction. This is due to the on-time delivery of products, the accurate fulfillment of orders, and the reduced damage to products.
- Increased sales
The efficient operations of the logistics center help to increase sales for Lawrence Foods Inc. This is due to the improved customer satisfaction, the reduced costs, and the ability to offer faster delivery times.
Overall, the efficient operations of Lawrence Foods Inc.’s logistics center are essential for the company’s success. The center’s efficient operations help to reduce costs, improve customer satisfaction, and increase sales.
4. Accurate order fulfillment
Accurate order fulfillment is a critical aspect of the Lawrence Foods Inc. logistics center. It ensures that customers receive the correct products, in the correct quantities, and on time. This is essential for maintaining customer satisfaction and loyalty.
- Complete and accurate orders
The logistics center uses a variety of methods to ensure that orders are complete and accurate. These methods include barcode scanning, RFID technology, and voice-directed picking. These technologies help to reduce errors and ensure that customers receive the products they ordered.
- On-time delivery
The logistics center works closely with its transportation providers to ensure that orders are delivered on time. The center uses a variety of shipping methods, including LTL, truckload, and air freight, to meet the needs of its customers. The center also has a team of dedicated customer service representatives who are available to track orders and provide updates to customers.
- Damage-free delivery
The logistics center takes great care to ensure that products are delivered damage-free. The center uses a variety of packaging materials and shipping methods to protect products from damage. The center also has a team of dedicated quality control inspectors who inspect products before they are shipped.
- Customer satisfaction
The logistics center’s focus on accurate order fulfillment has led to high levels of customer satisfaction. Customers know that they can rely on Lawrence Foods Inc. to deliver the right products, on time, and in good condition. This has helped Lawrence Foods Inc. to build a strong reputation for quality and service.
Accurate order fulfillment is essential for the success of the Lawrence Foods Inc. logistics center. By focusing on accuracy, the center is able to meet the needs of its customers and maintain high levels of customer satisfaction.
5. High food safety standards
Lawrence Foods Inc.’s logistics center adheres to the highest standards of food safety and quality control, ensuring that products are stored and handled in optimal conditions. This commitment to food safety is essential for maintaining the health and well-being of consumers, as well as for protecting the company’s reputation.
- HACCP certification
The logistics center is HACCP certified, which means that it has implemented a Hazard Analysis and Critical Control Points (HACCP) system. HACCP is a preventive food safety system that helps to identify, evaluate, and control hazards that could occur during the production, storage, and distribution of food.
- GMP compliance
The logistics center also complies with all Good Manufacturing Practices (GMP) regulations. GMPs are a set of regulations that govern the production, storage, and distribution of food. GMPs help to ensure that food is produced and handled in a sanitary and safe manner.
- Regular inspections
The logistics center is regularly inspected by government agencies to ensure that it is meeting all food safety standards. These inspections help to identify any areas where the center can improve its food safety practices.
- Employee training
All employees of the logistics center are trained in food safety practices. This training helps to ensure that employees understand the importance of food safety and that they are following all of the company’s food safety procedures.
Lawrence Foods Inc.’s commitment to food safety is evident in all aspects of its logistics center operations. The center’s HACCP certification, GMP compliance, regular inspections, and employee training all contribute to ensuring that food is stored and handled in a safe and sanitary manner. This commitment to food safety is essential for maintaining the health and well-being of consumers, as well as for protecting the company’s reputation.
6. Quality control
Quality control is a vital component of the Lawrence Foods Inc. logistics center. It ensures that products are stored and handled in a manner that maintains their quality and safety. This is essential for protecting the health and well-being of consumers, as well as for protecting the company’s reputation.
The logistics center has a dedicated team of quality control inspectors who are responsible for monitoring all aspects of the operation, from receiving and storage to shipping and delivery. These inspectors use a variety of methods to ensure that products meet the company’s high standards for quality, including:
- Visual inspections
- Temperature monitoring
- Microbiological testing
- Chemical testing
The quality control team also works closely with suppliers to ensure that products are meeting specifications before they are accepted into the logistics center. This includes conducting supplier audits and reviewing product documentation.
The Lawrence Foods Inc. logistics center’s commitment to quality control has resulted in a number of benefits for the company, including:
- Reduced product recalls
- Increased customer satisfaction
- Improved brand reputation
- Increased sales
Overall, quality control is a critical component of the Lawrence Foods Inc. logistics center. It helps to ensure that products are safe and high-quality, which is essential for protecting the health and well-being of consumers, as well as for protecting the company’s reputation.
7. Customer satisfaction
Customer satisfaction is a key component of the success of any business, and the Lawrence Foods Inc. logistics center is no exception. The center’s focus on customer satisfaction is evident in all aspects of its operations, from the efficient and accurate fulfillment of orders to the high standards of food safety and quality control. As a result, the logistics center has a high customer satisfaction rating, which has led to increased sales and improved brand reputation.
- Efficient and accurate order fulfillment
The logistics center’s efficient and accurate order fulfillment process helps to ensure that customers receive the right products, in the right quantities, and on time. This is essential for customer satisfaction, as customers want to know that they can rely on Lawrence Foods Inc. to deliver the products they need, when they need them.
- High standards of food safety and quality control
The logistics center’s high standards of food safety and quality control ensure that products are stored and handled in a safe and sanitary manner. This is essential for customer satisfaction, as customers want to know that the food they are eating is safe and of high quality.
- Responsive customer service
The logistics center’s responsive customer service team is available to answer customer questions and resolve any issues that may arise. This helps to ensure that customers are satisfied with their experience with Lawrence Foods Inc. and that they are likely to do business with the company again.
- Continuous improvement
The logistics center is committed to continuous improvement, and regularly reviews its operations to identify areas where it can improve customer satisfaction. This commitment to improvement helps to ensure that the logistics center is always meeting the needs of its customers.
Overall, the Lawrence Foods Inc. logistics center’s focus on customer satisfaction is evident in all aspects of its operations. The center’s efficient and accurate order fulfillment process, high standards of food safety and quality control, responsive customer service team, and commitment to continuous improvement all contribute to customer satisfaction. As a result, the logistics center has a high customer satisfaction rating, which has led to increased sales and improved brand reputation.
8. Competitive advantage
In today’s competitive business environment, companies are constantly looking for ways to gain a competitive advantage over their rivals. For Lawrence Foods Inc., the logistics center is a key source of competitive advantage. The center’s efficient operations, high standards of food safety and quality control, and focus on customer satisfaction all contribute to the company’s ability to compete successfully in the marketplace.
- Efficient operations
The Lawrence Foods Inc. logistics center is one of the most efficient in the industry. The center’s use of advanced technology, well-trained staff, and optimized processes allows the company to fulfill orders quickly and accurately. This efficiency gives Lawrence Foods Inc. a competitive advantage by reducing costs and improving customer satisfaction.
- High standards of food safety and quality control
Lawrence Foods Inc. is committed to providing its customers with safe, high-quality food products. The company’s logistics center adheres to the highest standards of food safety and quality control, which ensures that products are stored and handled in a sanitary and safe manner. This commitment to food safety gives Lawrence Foods Inc. a competitive advantage by protecting the health and well-being of its customers.
- Focus on customer satisfaction
Lawrence Foods Inc. is focused on providing its customers with the best possible experience. The company’s logistics center plays a key role in this effort by ensuring that orders are fulfilled accurately and on time. The center’s responsive customer service team is also available to answer questions and resolve any issues that may arise. This focus on customer satisfaction gives Lawrence Foods Inc. a competitive advantage by building strong relationships with its customers.
Overall, the Lawrence Foods Inc. logistics center is a key source of competitive advantage for the company. The center’s efficient operations, high standards of food safety and quality control, and focus on customer satisfaction all contribute to the company’s ability to compete successfully in the marketplace.
9. Growth potential
The growth potential of the Lawrence Foods Inc. logistics center is significant. The center is located in a strategic location with access to major transportation routes, which allows the company to quickly and efficiently distribute its products to customers throughout the region. The center is also equipped with advanced technology and efficient operations, which enable the company to fulfill orders accurately and on time. In addition, the center’s focus on customer satisfaction has led to high levels of customer loyalty.
As the demand for food and beverage products continues to grow, the Lawrence Foods Inc. logistics center is well-positioned to capitalize on this growth. The center’s strategic location, advanced technology, efficient operations, and focus on customer satisfaction will all contribute to the company’s ability to grow its market share and increase its profitability.
In addition, the Lawrence Foods Inc. logistics center is a key component of the company’s growth strategy. The center allows the company to quickly and efficiently distribute its products to new markets, and it also provides the company with the flexibility to meet the changing demands of its customers. As a result, the logistics center is essential for the company’s continued growth and success.
FAQs about Lawrence Foods Inc. Logistics Center
This section provides answers to frequently asked questions about the Lawrence Foods Inc. logistics center. These questions cover various aspects of the center’s operations, including its location, technology, and commitment to quality.
Question 1: Where is the Lawrence Foods Inc. logistics center located?
Answer: The Lawrence Foods Inc. logistics center is located in the heart of the Midwest, providing easy access to major transportation routes and allowing for efficient distribution of products throughout the region.
Question 2: What kind of technology is used in the logistics center?
Answer: The logistics center is equipped with advanced technology, including automated systems, advanced inventory management software, RFID technology, and voice-directed picking. This technology enhances efficiency, accuracy, and labor productivity.
Question 3: How does the logistics center ensure food safety and quality?
Answer: The logistics center adheres to the highest standards of food safety and quality control. It is HACCP certified, GMP compliant, and undergoes regular inspections. The staff is trained in food safety practices, and products are stored and handled in optimal conditions to maintain their quality and safety.
Question 4: How does the logistics center contribute to customer satisfaction?
Answer: The logistics center plays a crucial role in customer satisfaction by ensuring efficient and accurate order fulfillment, maintaining high standards of food safety and quality, and providing responsive customer service. These factors collectively contribute to building strong customer relationships and enhancing overall satisfaction.
Question 5: How does the logistics center support the growth of Lawrence Foods Inc.?
Answer: The logistics center is a key driver of Lawrence Foods Inc.’s growth strategy. Its strategic location, advanced technology, efficient operations, and focus on customer satisfaction enable the company to expand into new markets, meet changing customer demands, and increase profitability.
Question 6: What are the key benefits of using the Lawrence Foods Inc. logistics center?
Answer: The key benefits of using the Lawrence Foods Inc. logistics center include reduced costs, improved customer satisfaction, increased sales, enhanced food safety and quality, and support for the company’s growth strategy.
Summary: The Lawrence Foods Inc. logistics center is a state-of-the-art facility that leverages technology and best practices to ensure efficient operations, maintain high standards of food safety and quality, and contribute to overall customer satisfaction and the growth of the company.
Transition: To learn more about the Lawrence Foods Inc. logistics center and its commitment to excellence, please visit the company’s website or contact their customer service team.
Tips for Utilizing the Lawrence Foods Inc. Logistics Center
The Lawrence Foods Inc. logistics center offers a range of benefits to its customers, including efficient operations, high standards of food safety and quality, and a focus on customer satisfaction. To maximize the value derived from using the logistics center, consider implementing the following tips:
Tip 1: Plan ahead and provide accurate forecasts:
Providing accurate demand forecasts to the logistics center enables efficient inventory management and reduces the risk of stockouts or excess inventory.Tip 2: Leverage technology for seamless communication:
Utilizing the logistics center’s online portal or EDI (Electronic Data Interchange) system facilitates real-time order tracking, inventory visibility, and automated communication, enhancing supply chain efficiency.Tip 3: Maintain open communication and strong relationships:
Regular communication with the logistics center team fosters strong relationships and ensures that both parties are aligned on goals and expectations. Open dialogue allows for timely resolution of any challenges or adjustments to meet changing needs.Tip 4: Adhere to food safety and quality guidelines:
Complying with the logistics center’s food safety and quality standards ensures the integrity and quality of products throughout the supply chain. Following established guidelines minimizes the risk of contamination or product recalls.Tip 5: Utilize value-added services to enhance efficiency:
Exploring value-added services offered by the logistics center, such as labeling, kitting, or cross-docking, can streamline operations and reduce costs for businesses.Tip 6: Seek continuous improvement opportunities:
Regularly reviewing and evaluating the logistics processes with the center’s team identifies areas for improvement and optimization. Embracing a culture of continuous improvement leads to enhanced efficiency and cost savings.
By implementing these tips, businesses can effectively utilize the Lawrence Foods Inc. logistics center to optimize their supply chains, enhance customer satisfaction, and drive growth.
Conclusion: The Lawrence Foods Inc. logistics center is a strategic asset for businesses seeking to improve their logistics operations. By leveraging the center’s capabilities and adhering to these tips, companies can maximize the value they derive from this partnership, ultimately contributing to their overall success.
Conclusion
The Lawrence Foods Inc. logistics center is a crucial component of the company’s operations, enabling efficient storage, handling, and distribution of food and beverage products. Its strategic location, advanced technology, and commitment to food safety, quality, and customer satisfaction make it a valuable asset for the company and its customers.
The center’s efficient operations and accurate order fulfillment contribute to reduced costs, improved customer satisfaction, and increased sales for Lawrence Foods Inc. Its adherence to the highest standards of food safety and quality control ensures the health and well-being of consumers, while its focus on customer satisfaction fosters strong relationships and repeat business.
As the demand for food and beverage products continues to grow, the Lawrence Foods Inc. logistics center is well-positioned to support the company’s future growth and success. Its strategic location, advanced technology, efficient operations, and focus on customer satisfaction will enable the center to continue playing a vital role in the company’s supply chain and overall success.