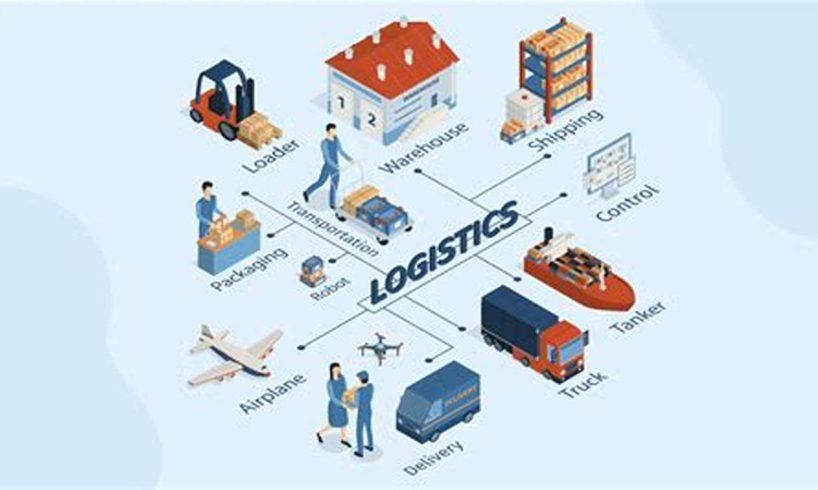
Logistic track refers to the streamlined management and coordination of resources, activities, and information throughout a supply chain. It involves planning, organizing, and controlling the flow of goods, services, and related information from the point of origin to the point of consumption.
An efficient logistic track is crucial for businesses to optimize their supply chain operations, reduce costs, improve customer service, and gain a competitive advantage. It enables businesses to track the movement of goods in real-time, identify potential bottlenecks, and make informed decisions to mitigate risks and improve efficiency.
The concept of logistic track has evolved over time with the advancement of technology. In the past, logistic activities were primarily manual and paper-based, but today, businesses leverage sophisticated software and digital platforms to automate and optimize their logistic processes. This has led to increased visibility, improved coordination, and enhanced decision-making capabilities within the supply chain.
1. Planning in Logistic Track
Planning is a fundamental component of logistic track, providing a roadmap for efficient and effective management of supply chain activities. It involves determining the best course of action to achieve logistic goals, considering various factors such as demand forecasting, inventory management, transportation optimization, and customer service requirements.
- Demand Forecasting
Demand forecasting is crucial for planning logistic operations. Businesses need to accurately predict future demand to ensure they have the right amount of inventory to meet customer needs without overstocking or experiencing stockouts. Advanced analytics and historical data analysis are used to develop demand forecasts that guide production, inventory management, and transportation planning.
- Inventory Management
Inventory management is another key aspect of logistic track planning. Businesses need to determine the optimal levels of inventory to hold to meet customer demand while minimizing storage costs and the risk of obsolescence. Effective inventory management involves balancing supply and demand, implementing inventory control techniques, and optimizing warehouse operations.
- Transportation Optimization
Transportation optimization is essential for efficient and cost-effective movement of goods. Logistic track planning involves selecting the most appropriate transportation modes, carriers, and routes to minimize transit times, reduce shipping costs, and ensure timely delivery to customers.
- Customer Service
Customer service is a critical factor in logistic track planning. Businesses need to consider customer expectations, delivery timeframes, and order fulfillment processes to ensure a seamless and satisfactory customer experience. Logistic track planning should align with customer service goals, such as fast and reliable delivery, accurate order processing, and responsive customer support.
By effectively planning these facets, businesses can lay the foundation for a robust and efficient logistic track that meets customer demands, optimizes resources, and contributes to overall business success.
2. Organizing in Logistic Track
Organizing is a crucial aspect of logistic track, involving the structuring of resources and activities to execute the logistic plan effectively. It encompasses various facets that contribute to the overall efficiency and coordination of the supply chain.
- Centralized Management
Centralized management is a common organizational structure in logistic track, where a central authority or control tower oversees and coordinates all logistic activities. This approach enables visibility, standardization, and efficient decision-making across the supply chain, ensuring alignment with the overall logistic plan.
- Cross-Functional Collaboration
Effective logistic track requires collaboration among various departments and functions within an organization. Cross-functional teams, involving members from sales, marketing, operations, and finance, work together to align logistic activities with the overall business goals and customer.
- Standardized Processes
Standardization of logistic processes is essential for efficient and consistent operations. By establishing clear and documented procedures, businesses can streamline activities, reduce errors, and improve overall supply chain performance.
- Resource Allocation
Organizing in logistic track also involves allocating resources effectively to support logistic activities. This includes determining the optimal number of warehouses, managing transportation resources, and ensuring adequate staffing levels to meet demand and minimize costs.
By effectively organizing these facets, businesses can create a well-structured and efficient logistic track that supports their overall business objectives, optimizes resource utilization, and enhances supply chain performance.
3. Controlling
Controlling is a critical component of logistic track, ensuring that logistic activities align with the overall plan and desired outcomes. It involves monitoring, evaluating, and adjusting logistic operations to maintain efficiency, minimize risks, and achieve customer satisfaction.
Effective controlling in logistic track requires real-time visibility into supply chain operations. This can be achieved through the use of technology, such as supply chain management (SCM) software and data analytics tools, which provide insights into inventory levels, order fulfillment status, and transportation performance. By monitoring these metrics, businesses can identify potential problems and take corrective actions to mitigate risks and ensure smooth logistic operations.
Controlling also involves regular performance evaluations to assess the effectiveness of logistic activities. This includes measuring key performance indicators (KPIs) such as inventory turnover, order fulfillment rates, and transportation costs. By comparing actual performance against targets, businesses can identify areas for improvement and make necessary adjustments to their logistic track.
The practical significance of controlling in logistic track cannot be overstated. Effective controlling enables businesses to:
- Reduce costs and improve efficiency by identifying and eliminating waste and redundancies in logistic operations.
- Enhance customer satisfaction by ensuring timely and accurate order fulfillment, as well as responsive customer service.
- Mitigate risks by proactively identifying and addressing potential disruptions or challenges in the supply chain.
In conclusion, controlling is an essential component of logistic track that enables businesses to monitor, evaluate, and adjust their logistic activities to achieve optimal performance, reduce costs, and enhance customer satisfaction.
4. Flow of Goods
The flow of goods is a crucial aspect of logistic track, encompassing the physical movement and exchange of items within a supply chain. It involves managing the movement of goods from suppliers to manufacturers, warehouses, distribution centers, and ultimately to end consumers. An efficient flow of goods is essential for businesses to meet customer demand, optimize inventory levels, and minimize transportation costs.
- Inventory Management
Inventory management is closely tied to the flow of goods, as it involves controlling the levels of inventory to ensure product availability while minimizing holding costs. Effective inventory management practices, such as just-in-time (JIT) inventory and safety stock optimization, can help businesses maintain an optimal flow of goods.
- Transportation Planning
Transportation planning is another key facet of the flow of goods. Businesses need to determine the most efficient and cost-effective modes of transportation, as well as plan transportation routes and schedules to ensure timely delivery of goods. Factors such as transportation costs, transit times, and reliability of carriers are considered in transportation planning.
- Order Fulfillment
Order fulfillment is the process of picking, packing, and shipping customer orders. An efficient order fulfillment process is essential for meeting customer expectations and maintaining a positive customer experience. Logistic track plays a critical role in order fulfillment by ensuring the availability of goods, optimizing picking and packing operations, and coordinating with carriers for timely delivery.
- Reverse Logistics
Reverse logistics involves the management of returned goods, defective products, and end-of-life items. Logistic track can help businesses optimize reverse logistics processes by establishing efficient return policies, coordinating with suppliers for product recalls, and managing the disposal or recycling of returned goods.
In conclusion, the flow of goods is a fundamental component of logistic track, encompassing various facets such as inventory management, transportation planning, order fulfillment, and reverse logistics. Efficient management of the flow of goods is essential for businesses to achieve supply chain optimization, reduce costs, and enhance customer satisfaction.
5. Flow of services
The flow of services is a crucial component of logistic track, encompassing the movement and delivery of services to customers. Services can range from consulting and technical support to maintenance and repair, and they play a vital role in various industries, including manufacturing, healthcare, and information technology.
In the context of logistic track, the flow of services involves managing the movement of service providers, equipment, and information to ensure timely and efficient delivery of services to customers. This includes scheduling appointments, dispatching service technicians, tracking progress, and managing customer communication. Effective management of the flow of services is essential for businesses to meet customers, optimize resource utilization, and enhance customer satisfaction.
One real-life example of the flow of services in logistic track is field service management. In industries such as telecommunications and utilities, technicians are dispatched to customer locations to perform maintenance, repairs, or installations. Logistic track plays a critical role in managing the flow of these services by optimizing technician schedules, providing real-time visibility into technician locations and availability, and ensuring efficient communication between technicians and customers.
The practical significance of understanding the flow of services in logistic track lies in its ability to improve service delivery, reduce costs, and enhance customer satisfaction. By optimizing the flow of services, businesses can ensure that the right service providers are dispatched to the right location at the right time, minimizing downtime and improving customer responsiveness. This can lead to increased customer satisfaction, reduced costs associated with service delivery, and a competitive advantage in the marketplace.
6. Flow of Information
The flow of information is a crucial aspect of logistic track, as it enables the timely and accurate exchange of data throughout the supply chain. It involves the collection, processing, and sharing of information related to inventory levels, order status, shipment tracking, and customer data. Efficient management of the flow of information is essential for businesses to make informed decisions, optimize operations, and provide excellent customer service.
- Inventory Management
The flow of information plays a vital role in inventory management by providing real-time visibility into inventory levels across different locations. This information helps businesses optimize stock levels, avoid stockouts, and reduce carrying costs. Advanced inventory management systems leverage data analytics to forecast demand, generate replenishment orders, and track inventory movement in real time.
- Order Fulfillment
The flow of information is essential for efficient order fulfillment. It enables businesses to track the status of orders, monitor progress through the fulfillment process, and provide accurate delivery ETAs to customers. Real-time information sharing between different departments, such as sales, inventory, and shipping, ensures smooth coordination and timely order delivery.
- Shipment Tracking
The flow of information allows businesses to track the movement of shipments in real time. This information is shared with customers to provide visibility into the delivery status of their orders. Advanced tracking systems use GPS technology and data analytics to monitor the location of shipments and provide estimated delivery times. This enhances customer satisfaction and reduces the need for manual tracking efforts.
- Customer Communication
The flow of information is crucial for effective customer communication. It enables businesses to keep customers informed about order status updates, delivery schedules, and any potential delays or issues. Timely and accurate communication helps build trust and transparency with customers, leading to improved customer satisfaction and loyalty.
In conclusion, the effective management of the flow of information is essential for efficient logistic track. By leveraging real-time data and advanced information systems, businesses can optimize inventory management, enhance order fulfillment, improve shipment tracking, and provide excellent customer communication. This leads to improved supply chain performance, reduced costs, and increased customer satisfaction.
7. Supply Chain Visibility
Supply chain visibility is a critical aspect of logistic track, providing real-time insights into the location and status of goods, services, and related information throughout the supply chain. It enables businesses to monitor inventory levels, track shipments, and manage orders more effectively, leading to improved supply chain performance and customer satisfaction.
- Inventory Visibility
Inventory visibility provides real-time information about inventory levels across different locations, including warehouses, distribution centers, and retail stores. This information helps businesses optimize stock levels, avoid stockouts, and reduce carrying costs. Advanced inventory management systems leverage data analytics to forecast demand, generate replenishment orders, and track inventory movement in real time.
- Shipment Tracking
Shipment tracking allows businesses to monitor the movement of shipments in real time, from the point of origin to the point of delivery. This information is shared with customers to provide visibility into the delivery status of their orders. Advanced tracking systems use GPS technology and data analytics to monitor the location of shipments and provide estimated delivery times. This enhances customer satisfaction and reduces the need for manual tracking efforts.
- Order Status Tracking
Order status tracking provides real-time updates on the status of orders, from the moment they are placed to the moment they are delivered. This information helps businesses monitor progress through the fulfillment process and identify any potential delays or issues. Real-time information sharing between different departments, such as sales, inventory, and shipping, ensures smooth coordination and timely order delivery.
- Supplier Performance Monitoring
Supplier performance monitoring provides visibility into the performance of suppliers, including their delivery times, quality standards, and responsiveness. This information helps businesses evaluate supplier reliability, identify potential risks, and make informed decisions about supplier selection and management. By monitoring supplier performance, businesses can minimize supply chain disruptions and ensure the smooth flow of goods and services.
Supply chain visibility is a key enabler for efficient logistic track. By providing real-time insights into the supply chain, businesses can make informed decisions, optimize operations, and improve customer service. This leads to reduced costs, increased efficiency, and enhanced overall supply chain performance.
8. Risk Mitigation in Logistic Track
Risk mitigation plays a crucial role in logistic track, as it enables businesses to identify, assess, and manage potential risks that could disrupt supply chain operations and impact customer service. By proactively addressing risks, businesses can minimize their negative consequences, ensure the smooth flow of goods and services, and protect their overall profitability.
- Risk Identification
The first step in risk mitigation is identifying potential risks that could affect logistic operations. These risks can be internal, such as equipment failures or human errors, or external, such as natural disasters or changes in regulations. Thorough risk assessments help businesses understand the likelihood and impact of potential risks, allowing them to prioritize and develop appropriate mitigation strategies.
- Risk Assessment
Once risks have been identified, they need to be assessed to determine their potential impact on logistic operations. This involves evaluating the severity of the risk, the likelihood of it occurring, and the potential financial and reputational consequences. Risk assessment helps businesses prioritize risks and allocate resources accordingly.
- Risk Mitigation Strategies
Based on the risk assessment, businesses can develop and implement risk mitigation strategies to reduce the likelihood and impact of potential risks. These strategies can include diversifying suppliers, implementing backup plans, investing in technology, and training employees. Effective risk mitigation strategies help businesses minimize disruptions, protect their supply chain, and ensure the continuous flow of goods and services.
- Contingency Planning
Contingency planning is an essential aspect of risk mitigation in logistic track. It involves developing plans to respond to and recover from unexpected events that could disrupt supply chain operations. Contingency plans outline alternative courses of action, identify key personnel and resources, and establish communication protocols. By having contingency plans in place, businesses can minimize the impact of disruptions and ensure a rapid recovery.
Effective risk mitigation in logistic track is essential for businesses to maintain supply chain resilience, protect their reputation, and achieve long-term success. By proactively identifying, assessing, and mitigating risks, businesses can minimize disruptions, optimize operations, and enhance customer satisfaction.
9. Customer service
Customer service is a crucial component of logistic track, directly impacting customer satisfaction, brand reputation, and overall business success. Effective customer service ensures that customers’ needs and expectations are met throughout their interactions with the logistic track, resulting in positive experiences and long-term loyalty.
One of the primary connections between customer service and logistic track lies in order fulfillment. Efficient and timely order fulfillment is essential for meeting customer expectations and building trust. Logistic track plays a vital role in ensuring that orders are processed accurately, shipped promptly, and delivered in good condition. Real-time tracking and proactive communication with customers provide visibility into the order status, enhancing customer satisfaction and reducing inquiries.
Moreover, customer service is instrumental in handling inquiries, resolving issues, and providing support to customers. A dedicated customer service team can address customer concerns promptly, provide accurate information, and offer solutions to problems that may arise during the delivery process. By resolving issues efficiently, customer service helps maintain customer satisfaction, mitigates negative feedback, and strengthens the overall customer experience.
The practical significance of understanding the connection between customer service and logistic track lies in its ability to drive business growth and profitability. Positive customer experiences lead to increased customer loyalty, repeat purchases, and positive word-of-mouth. By integrating customer service into logistic track and focusing on customer satisfaction, businesses can differentiate themselves in the competitive market and gain a competitive advantage.
FAQs on Logistic Track
This section addresses frequently asked questions and misconceptions about logistic track, providing clear and informative answers in a serious tone.
Question 1: What is the significance of logistic track in supply chain management?
Answer: Logistic track is crucial in supply chain management as it optimizes the flow of goods, services, and information throughout the chain. By streamlining processes, reducing costs, and improving customer service, it enhances the overall efficiency and effectiveness of supply chain operations.
Question 2: How does logistic track contribute to customer satisfaction?
Answer: Logistic track directly impacts customer satisfaction by ensuring timely and accurate order fulfillment, efficient handling of inquiries, and proactive resolution of issues. Positive customer experiences foster loyalty, repeat purchases, and positive word-of-mouth, contributing to business growth and profitability.
Question 3: What are the key components of a robust logistic track?
Answer: A robust logistic track encompasses planning, organizing, controlling, flow of goods, flow of services, flow of information, supply chain visibility, risk mitigation, and customer service. Each component plays a vital role in optimizing supply chain operations and achieving desired outcomes.
Question 4: How does technology enhance logistic track?
Answer: Technology plays a transformative role in logistic track by automating processes, providing real-time visibility, and enabling data-driven decision-making. Advanced systems, such as transportation management systems (TMS) and warehouse management systems (WMS), optimize resource allocation, reduce manual errors, and improve overall operational efficiency.
Question 5: What are the challenges associated with logistic track?
Answer: Logistic track faces challenges such as supply chain disruptions, demand fluctuations, and global economic uncertainties. Effective logistic track requires adaptability, contingency planning, and continuous improvement efforts to overcome these challenges and maintain operational resilience.
Question 6: How can businesses measure the effectiveness of their logistic track?
Answer: Key performance indicators (KPIs) are used to measure the effectiveness of logistic track. Common KPIs include inventory turnover, order fulfillment rates, transportation costs, and customer satisfaction metrics. Regular monitoring and analysis of these KPIs enable businesses to identify areas for improvement and optimize their logistic track continuously.
Summary: Logistic track is a critical aspect of supply chain management that impacts various business functions and customer experiences. By addressing common questions and misconceptions, this FAQ section provides a clear understanding of its significance, components, challenges, and measurement techniques, enabling businesses to leverage logistic track effectively for improved supply chain performance.
Transition: The insights gained from this FAQ section lay the foundation for further exploration into the practical applications and benefits of logistic track in various industries and business contexts.
Tips for Logistic Track Optimization
In the dynamic world of supply chain management, optimizing logistic track is crucial for businesses to gain a competitive edge and enhance overall performance. Here are some valuable tips to help you streamline your logistic track:
Tip 1: Leverage Technology: Embrace technology to automate processes, gain real-time visibility, and improve decision-making. Implement transportation management systems (TMS), warehouse management systems (WMS), and other advanced solutions to optimize resource allocation, reduce errors, and enhance efficiency.
Tip 2: Enhance Supply Chain Visibility: Establish end-to-end supply chain visibility to track the movement of goods, inventory levels, and order status in real time. This enables proactive monitoring, identification of potential disruptions, and quick response to changing market demands.
Tip 3: Optimize Inventory Management: Implement robust inventory management strategies to maintain optimal stock levels, minimize carrying costs, and reduce the risk of stockouts. Leverage inventory optimization techniques, such as just-in-time (JIT) inventory and safety stock management, to improve inventory turnover and enhance cash flow.
Tip 4: Strengthen Supplier Relationships: Foster strong relationships with suppliers to ensure reliable and timely delivery of goods and services. Collaborate with suppliers to optimize lead times, establish clear communication channels, and implement supplier performance monitoring mechanisms to mitigate risks and improve overall supply chain efficiency.
Tip 5: Focus on Customer Service: Prioritize customer satisfaction by providing exceptional logistic services. Implement efficient order fulfillment processes, offer flexible delivery options, and establish a dedicated customer service team to promptly address inquiries and resolve issues, building customer loyalty and driving repeat business.
Tip 6: Monitor and Measure Performance: Regularly monitor and measure the performance of your logistic track using relevant key performance indicators (KPIs). Track metrics such as inventory turnover, order fulfillment rates, transportation costs, and customer satisfaction to identify areas for improvement and make data-driven decisions to optimize your operations continuously.
Summary: By implementing these tips, businesses can significantly enhance their logistic track, leading to improved supply chain performance, reduced costs, increased customer satisfaction, and a competitive advantage in the marketplace.
Transition: To further delve into the benefits of logistic track optimization, let’s explore some real-world examples of how businesses have leveraged these strategies to achieve remarkable results.
Conclusion
Throughout this exploration, we have gained a comprehensive understanding of logistic track and its critical role in supply chain management. From planning and organizing to controlling and monitoring, each aspect plays a vital role in optimizing the flow of goods, services, and information.
By leveraging technology, enhancing supply chain visibility, optimizing inventory management, strengthening supplier relationships, focusing on customer service, and continuously measuring performance, businesses can significantly improve their logistic track. This leads to reduced costs, increased efficiency, enhanced customer satisfaction, and a competitive edge in today’s global marketplace.