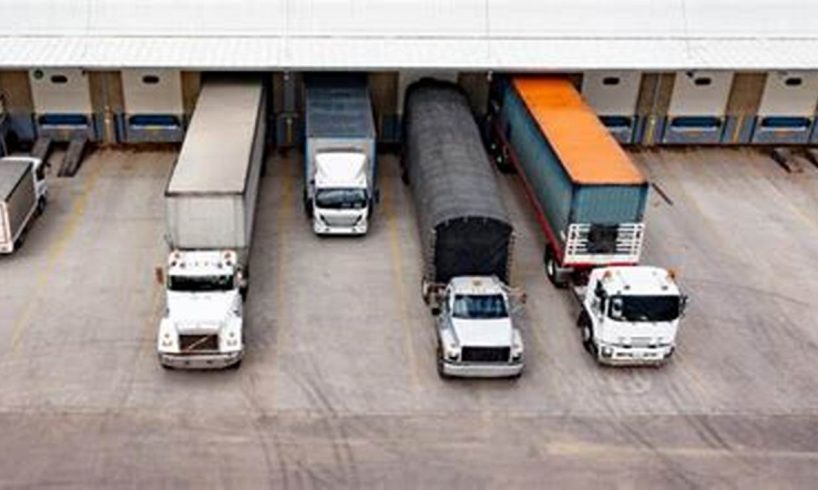
Managed receiving capstone logistics is a comprehensive approach to managing the receiving process, ensuring accuracy, efficiency, and cost-effectiveness. It involves a set of best practices and technologies that streamline the receiving process, from the initial receipt of goods to their storage and distribution.
Managed receiving capstone logistics is crucial for businesses of all sizes, but it is particularly beneficial for those that receive high volumes of goods or have complex supply chains. By implementing managed receiving capstone logistics, businesses can improve their inventory accuracy, reduce their receiving costs, and improve their customer service levels.
The main topics covered in this article include:
- The benefits of managed receiving capstone logistics
- The key components of managed receiving capstone logistics
- How to implement managed receiving capstone logistics in your business
1. Visibility
Visibility is a key component of managed receiving capstone logistics. It provides businesses with a real-time view of their receiving process, allowing them to track the status of their shipments and identify any potential delays or problems. This visibility is essential for businesses that want to improve their inventory accuracy, reduce their receiving costs, and improve their customer service levels.
There are a number of ways to achieve visibility into the receiving process. One common method is to use a warehouse management system (WMS). A WMS can provide businesses with a real-time view of their inventory, as well as the status of their shipments. This information can be used to identify potential delays or problems, and to take corrective action.
Another way to achieve visibility into the receiving process is to use radio frequency identification (RFID) technology. RFID tags can be attached to shipments, and then tracked using RFID readers. This information can be used to track the status of shipments, and to identify any potential delays or problems.Visibility is an essential component of managed receiving capstone logistics. By implementing visibility into their receiving process, businesses can improve their inventory accuracy, reduce their receiving costs, and improve their customer service levels.
Here are some examples of how visibility can be used to improve the receiving process:
- A business can use visibility to identify shipments that are delayed or at risk of being delayed. This information can be used to take corrective action, such as rerouting the shipment or expediting the delivery.
- A business can use visibility to identify shipments that have been damaged or lost. This information can be used to file a claim with the carrier and to take steps to prevent future damage or loss.
- A business can use visibility to track the status of shipments that are being returned to the supplier. This information can be used to expedite the return process and to ensure that the supplier receives the returned goods in a timely manner.
Visibility is a powerful tool that can be used to improve the receiving process. By implementing visibility into their receiving process, businesses can improve their inventory accuracy, reduce their receiving costs, and improve their customer service levels.
2. Accuracy
Accuracy is essential in managed receiving capstone logistics. It ensures that businesses receive the correct products, in the correct quantities, and in the correct condition. This is important for a number of reasons, including:
- Inventory accuracy: Accurate receiving helps to ensure that businesses have accurate inventory records. This is important for a number of reasons, including planning production, managing inventory levels, and fulfilling customer orders.
- Cost reduction: Accurate receiving can help to reduce costs by reducing the number of errors and omissions that occur during the receiving process. This can lead to reduced waste, reduced shipping costs, and reduced labor costs.
- Improved customer service: Accurate receiving can help to improve customer service by ensuring that customers receive the correct products, in the correct quantities, and in the correct condition. This can lead to increased customer satisfaction and loyalty.
There are a number of ways to improve the accuracy of the receiving process. Some of the most common methods include:
- Using a barcode scanner: Barcode scanners can be used to quickly and accurately identify products as they are received. This can help to reduce errors that occur when products are manually entered into the system.
- Using a receiving management system: A receiving management system can help to automate the receiving process and reduce errors. These systems can be used to track shipments, generate receiving reports, and manage inventory levels.
- Training staff: Training staff on the proper receiving procedures can help to reduce errors. Staff should be trained on how to identify products, how to enter data into the system, and how to handle damaged or missing products.
By implementing these strategies, businesses can improve the accuracy of their receiving process and reap the benefits that come with it.
3. Efficiency
Efficiency is a key component of managed receiving capstone logistics. It is the ability to complete the receiving process quickly and accurately, with minimal waste and effort. Managed receiving capstone logistics can help to improve the efficiency of the receiving process by automating tasks and streamlining workflows.
One way that managed receiving capstone logistics can improve efficiency is by automating tasks. For example, a receiving management system can be used to automate the following tasks:
- Receiving shipments
- Generating receiving reports
- Managing inventory levels
By automating these tasks, businesses can free up their staff to focus on other value-added activities, such as customer service or quality control.
Another way that managed receiving capstone logistics can improve efficiency is by streamlining workflows. For example, a business can implement a first-in, first-out (FIFO) inventory system to ensure that the oldest inventory is used first. This can help to reduce waste and improve the accuracy of the inventory records.
By implementing managed receiving capstone logistics, businesses can improve the efficiency of their receiving process and reap the benefits that come with it, such as reduced costs, improved customer service, and increased profitability.
Here are some real-life examples of how managed receiving capstone logistics has helped businesses to improve efficiency:
- A large retailer implemented a receiving management system to automate the receiving process. The system resulted in a 20% reduction in receiving time and a 15% reduction in receiving costs.
- A manufacturing company implemented a FIFO inventory system to reduce waste and improve inventory accuracy. The system resulted in a 10% reduction in waste and a 5% improvement in inventory accuracy.
These are just a few examples of how managed receiving capstone logistics can help businesses to improve efficiency. By implementing managed receiving capstone logistics, businesses can improve the accuracy of their receiving process, reduce their receiving costs, and improve their customer service levels.
4. Cost-effectiveness
Cost-effectiveness is a key consideration for any business, and managed receiving capstone logistics can help businesses to reduce their costs in a number of ways.
- Reduced labor costs: Managed receiving capstone logistics can help to reduce labor costs by automating tasks and streamlining workflows. For example, a receiving management system can be used to automate the following tasks:
- Receiving shipments
- Generating receiving reports
- Managing inventory levels
- Improved inventory management: Managed receiving capstone logistics can help to improve inventory management by providing businesses with real-time visibility into their inventory levels. This visibility can help businesses to reduce waste and improve the accuracy of their inventory records.
By reducing labor costs and improving inventory management, managed receiving capstone logistics can help businesses to reduce their overall costs and improve their profitability.
5. Compliance
Compliance is a critical aspect of managed receiving capstone logistics. Businesses that handle hazardous materials must comply with a variety of regulatory requirements, including those related to the storage, handling, and transportation of these materials. Managed receiving capstone logistics can help businesses to comply with these requirements by providing them with the tools and processes they need to manage hazardous materials safely and efficiently.
- Documentation: Managed receiving capstone logistics can help businesses to maintain accurate and up-to-date documentation on the hazardous materials they receive. This documentation can include safety data sheets (SDSs), inventory records, and training records.
- Training: Managed receiving capstone logistics can help businesses to provide their employees with the training they need to safely handle hazardous materials. This training can cover topics such as the proper storage and handling of hazardous materials, the use of personal protective equipment (PPE), and emergency response procedures.
- Inspections: Managed receiving capstone logistics can help businesses to conduct regular inspections of their hazardous materials storage and handling areas. These inspections can help to identify any potential hazards and ensure that the business is complying with all applicable regulatory requirements.
- Emergency response: Managed receiving capstone logistics can help businesses to develop and implement emergency response plans for hazardous materials incidents. These plans should include procedures for responding to spills, leaks, fires, and other emergencies.
By implementing managed receiving capstone logistics, businesses can improve their compliance with regulatory requirements and reduce their risk of accidents and fines. In addition, managed receiving capstone logistics can help businesses to improve their safety record and protect their employees, customers, and the environment.
6. Sustainability
Sustainability is a growing concern for businesses of all sizes. Consumers are increasingly demanding products and services that are produced in an environmentally responsible way. Managed receiving capstone logistics can help businesses to meet this demand by reducing waste and emissions.
One way that managed receiving capstone logistics can reduce waste is by improving inventory management. By implementing a just-in-time (JIT) inventory system, businesses can reduce the amount of inventory they have on hand. This can lead to reduced waste, as well as reduced storage costs.
Managed receiving capstone logistics can also reduce emissions by optimizing transportation routes. By using a transportation management system (TMS), businesses can plan their shipments in a way that minimizes the distance traveled. This can lead to reduced fuel consumption and emissions.
In addition, managed receiving capstone logistics can help businesses to identify and reduce packaging waste. By working with suppliers to use less packaging, businesses can reduce the amount of waste they generate.
Here are some real-life examples of how managed receiving capstone logistics has helped businesses to reduce their environmental impact:
- A large retailer implemented a JIT inventory system to reduce its inventory levels. The system resulted in a 20% reduction in waste and a 15% reduction in storage costs.
- A manufacturing company implemented a TMS to optimize its transportation routes. The system resulted in a 10% reduction in fuel consumption and emissions.
- A food distributor worked with its suppliers to reduce packaging waste. The company was able to reduce its packaging waste by 15%.
These are just a few examples of how managed receiving capstone logistics can help businesses to reduce their environmental impact. By implementing managed receiving capstone logistics, businesses can improve their sustainability performance and reduce their environmental impact.
7. Customer service
Managed receiving capstone logistics can improve customer service levels in a number of ways. First, it can help businesses to provide accurate and timely information about the status of shipments. This information can be used to keep customers informed about the progress of their orders and to resolve any issues that may arise.
- Improved communication: Managed receiving capstone logistics can help businesses to improve communication with their customers. By providing accurate and timely information about the status of shipments, businesses can keep customers informed about the progress of their orders and resolve any issues that may arise.
- Reduced customer inquiries: Managed receiving capstone logistics can help businesses to reduce the number of customer inquiries they receive. By providing customers with accurate and timely information about the status of their shipments, businesses can reduce the need for customers to call or email to inquire about their orders.
- Increased customer satisfaction: Managed receiving capstone logistics can help businesses to increase customer satisfaction. By providing accurate and timely information about the status of shipments, businesses can reduce the frustration that customers may experience when they are waiting for their orders.
Overall, managed receiving capstone logistics can help businesses to improve their customer service levels and increase customer satisfaction. By providing accurate and timely information about the status of shipments, businesses can keep customers informed, reduce customer inquiries, and increase customer satisfaction.
FAQs on Managed Receiving Capstone Logistics
This section presents commonly asked questions and their respective answers on managed receiving capstone logistics. These questions aim to address typical concerns, clear up misconceptions, and provide a deeper understanding of the topic.
Question 1: What is managed receiving capstone logistics?
Answer: Managed receiving capstone logistics refers to a comprehensive approach to managing the receiving process, encompassing best practices and technologies to enhance accuracy, efficiency, cost-effectiveness, and overall logistics performance.
Question 2: Why is managed receiving capstone logistics important?
Answer: Implementing managed receiving capstone logistics can bring numerous benefits, including improved inventory accuracy, reduced receiving costs, enhanced customer service, increased compliance, better sustainability practices, and streamlined communication.
Question 3: What components are involved in managed receiving capstone logistics?
Answer: Key components of managed receiving capstone logistics include visibility into the receiving process, accuracy measures to minimize errors, efficiency enhancements through automation and workflow optimization, cost-effective practices to reduce expenses, compliance with regulatory requirements, sustainability initiatives to lessen environmental impact, and improved customer service through timely and accurate shipment status updates.
Question 4: What are the advantages of implementing managed receiving capstone logistics?
Answer: Managed receiving capstone logistics offers a range of advantages, such as reduced labor costs, improved inventory management, enhanced compliance, better sustainability outcomes, and increased customer satisfaction due to accurate and timely shipment information.
Question 5: How can businesses effectively implement managed receiving capstone logistics?
Answer: Successful implementation involves evaluating current receiving processes, identifying areas for improvement, selecting appropriate technologies, training staff on new procedures, and continuously monitoring and adjusting the system to maintain optimal performance.
Question 6: What are some best practices for managed receiving capstone logistics?
Answer: Best practices include utilizing barcode scanners for accurate product identification, employing receiving management systems to automate tasks, implementing first-in, first-out (FIFO) inventory systems to minimize waste, and establishing clear communication channels for efficient information sharing.
In summary, managed receiving capstone logistics plays a crucial role in optimizing the receiving process within supply chains. By addressing common questions and concerns, this FAQ section has shed light on the importance, components, advantages, implementation strategies, and best practices associated with managed receiving capstone logistics.
Transition to the next article section: This comprehensive overview of managed receiving capstone logistics provides a solid foundation for further exploration into specific aspects of the topic.
Tips for Managed Receiving Capstone Logistics
Managed receiving capstone logistics involves a set of best practices and technologies to enhance the receiving process. Here are some tips to optimize your managed receiving capstone logistics:
Tip 1: Utilize Technology for Automation and Accuracy
Implement barcode scanners or radio frequency identification (RFID) technology to automate product identification and data entry. This reduces errors and improves the overall accuracy of the receiving process.
Tip 2: Establish Clear Communication Channels
Open and effective communication among stakeholders is crucial. Define clear roles and responsibilities, and establish designated communication channels to ensure timely and accurate information exchange.
Tip 3: Implement a Receiving Management System (RMS)
An RMS automates tasks such as shipment receiving, data entry, and inventory management. This streamlines the process, reduces manual labor, and improves efficiency.
Tip 4: Train Staff on Proper Procedures
Well-trained staff is essential for successful managed receiving capstone logistics. Provide comprehensive training on receiving procedures, safety protocols, and the use of any implemented technologies.
Tip 5: Regularly Monitor and Adjust
Continuously monitor your managed receiving capstone logistics performance to identify areas for improvement. Make necessary adjustments to processes, technologies, or training to maintain optimal efficiency.
Tip 6: Leverage First-In, First-Out (FIFO) Inventory Management
Implementing a FIFO system ensures that older inventory is used first, reducing waste and maintaining inventory accuracy.
Tip 7: Collaborate with Suppliers for Efficient Delivery
Establish clear expectations and communication channels with suppliers to ensure timely delivery of goods and accurate documentation.
Tip 8: Prioritize Sustainability Practices
Incorporate sustainable practices, such as reducing packaging waste and optimizing transportation routes, to minimize environmental impact.
By following these tips, businesses can effectively implement managed receiving capstone logistics to enhance accuracy, efficiency, cost-effectiveness, and overall supply chain performance.
Remember, a well-managed receiving process is crucial for seamless supply chain operations, improved customer satisfaction, and increased profitability.
Managed Receiving Capstone Logistics
Managed receiving capstone logistics has emerged as a cornerstone of supply chain management, offering a comprehensive approach to optimize the receiving process. By implementing best practices and leveraging technology, businesses can enhance accuracy, boost efficiency, reduce costs, ensure compliance, promote sustainability, and elevate customer service.
The key takeaways from this exploration of managed receiving capstone logistics include:
- Visibility into the receiving process empowers businesses with real-time tracking and proactive issue identification.
- Accuracy measures minimize errors and omissions, ensuring the integrity of inventory records.
- Efficiency enhancements through automation and streamlined workflows optimize resource utilization.
- Cost-effectiveness practices reduce labor expenses and improve inventory management, leading to increased profitability.
- Compliance with regulatory requirements safeguards businesses from legal liabilities and reputational risks.
- Sustainability initiatives lessen environmental impact and align with evolving customer expectations.
- Improved customer service through timely and accurate shipment status updates enhances customer satisfaction and loyalty.
Embracing managed receiving capstone logistics is not merely an operational improvement but a strategic investment in supply chain excellence. By adopting these practices, businesses can gain a competitive edge, mitigate risks, and drive long-term success in today’s dynamic and demanding business environment.