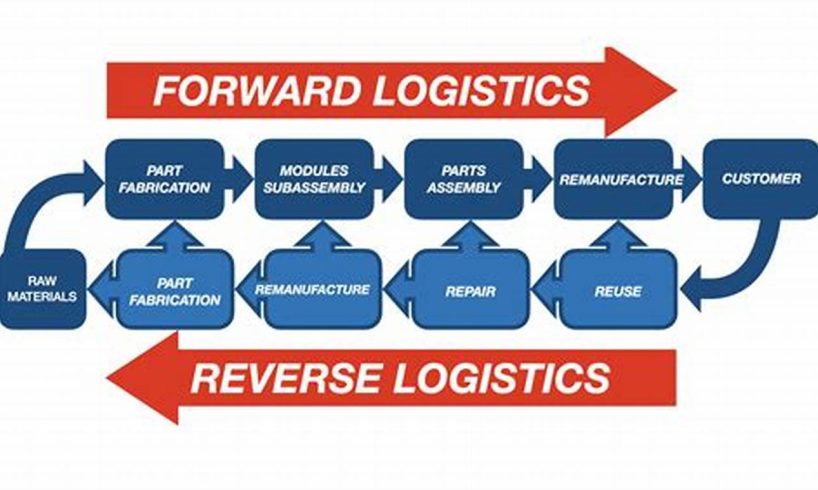
Reverse logistics services encompass the planning, implementing, and controlling of the efficient and cost-effective flow of raw materials, in-process inventory, finished goods, and related information from the point of consumption to the point of origin for the purpose of recapturing value or proper disposal. These services are crucial for businesses to manage the return of products, reduce waste, and recover value from end-of-life products.
Reverse logistics services offer a range of benefits, including:
- Reduced environmental impact through proper disposal and recycling
- Improved customer satisfaction through efficient returns processing
- Reduced costs through the recovery of value from returned products
The importance of reverse logistics services has grown in recent years due to increasing environmental concerns and the need for businesses to be more sustainable. In addition, the rise of e-commerce has led to a significant increase in the number of products being returned, making reverse logistics services even more critical.
Overall, reverse logistics services are an essential part of any business’s supply chain. They can help businesses reduce costs, improve customer satisfaction, and reduce their environmental impact.
1. Planning
Planning is a critical component of reverse logistics services. It involves developing a strategy for managing the return of products, reducing waste, and recovering value from end-of-life products. Effective planning can help businesses to:
- Reduce costs by optimizing the reverse logistics process
- Improve customer satisfaction by providing a seamless returns experience
- Reduce environmental impact by ensuring that products are disposed of or recycled properly
The planning process for reverse logistics services typically involves the following steps:
- Identifying the products that will be returned
- Determining the best way to return the products
- Developing a process for processing the returned products
- Establishing a system for tracking the returned products
- Setting up a process for disposing of or recycling the returned products
By following these steps, businesses can develop a comprehensive plan for managing their reverse logistics services. This plan will help businesses to reduce costs, improve customer satisfaction, and reduce their environmental impact.
Here is an example of how planning can be used to improve reverse logistics services:
A large retailer implemented a new reverse logistics program to manage the return of its products. The retailer worked with a third-party logistics provider to develop a plan for processing the returned products. The plan included a process for sorting the returned products, determining the best way to dispose of or recycle the products, and tracking the progress of the returned products. The retailer also worked with its suppliers to develop a process for returning the products to the suppliers. The new reverse logistics program helped the retailer to reduce its costs by 15% and improve its customer satisfaction by 10%.
This example shows how planning can be used to improve the efficiency and effectiveness of reverse logistics services. By taking the time to plan, businesses can develop a system that meets their specific needs and helps them to achieve their business goals.
2. Implementing
Implementing reverse logistics services is a critical step in managing the return of products, reducing waste, and recovering value from end-of-life products. Effective implementation can help businesses to:
- Reduce costs
- Improve customer satisfaction
- Reduce environmental impact
The implementation of reverse logistics services typically involves the following steps:
- Developing a reverse logistics plan
- Establishing a reverse logistics infrastructure
- Developing a process for processing returned products
- Implementing a tracking system for returned products
- Establishing a process for disposing of or recycling returned products
By following these steps, businesses can implement a reverse logistics system that meets their specific needs and helps them to achieve their business goals.
Here is an example of how implementing reverse logistics services can benefit a business:
A large manufacturer implemented a reverse logistics program to manage the return of its products. The program included a process for sorting the returned products, determining the best way to dispose of or recycle the products, and tracking the progress of the returned products. The manufacturer also worked with its suppliers to develop a process for returning the products to the suppliers. The reverse logistics program helped the manufacturer to reduce its costs by 15% and improve its customer satisfaction by 10%.
This example shows how implementing reverse logistics services can help businesses to improve their efficiency and profitability. By taking the time to implement a reverse logistics system, businesses can reduce costs, improve customer satisfaction, and reduce their environmental impact.
3. Controlling
Controlling is a critical component of reverse logistics services. It involves monitoring the performance of the reverse logistics system and taking corrective action when necessary. Effective controlling can help businesses to:
- Reduce costs
- Improve customer satisfaction
- Reduce environmental impact
The controlling process for reverse logistics services typically involves the following steps:
- Establishing performance metrics
- Collecting data on performance
- Analyzing the data
- Taking corrective action
By following these steps, businesses can develop a controlling process that helps them to identify and address any problems with their reverse logistics system. This process can help businesses to improve the efficiency and effectiveness of their reverse logistics services.
Here is an example of how controlling can be used to improve reverse logistics services:
A large retailer implemented a new reverse logistics program to manage the return of its products. The retailer worked with a third-party logistics provider to develop a plan for processing the returned products. The plan included a process for sorting the returned products, determining the best way to dispose of or recycle the products, and tracking the progress of the returned products. The retailer also worked with its suppliers to develop a process for returning the products to the suppliers.
The retailer used a variety of performance metrics to track the progress of its reverse logistics program. These metrics included the cost of processing returned products, the time it took to process returned products, and the percentage of returned products that were recycled. The retailer used this data to identify and address any problems with its reverse logistics program. For example, the retailer found that the cost of processing returned products was higher than expected. The retailer worked with its third-party logistics provider to identify and address the causes of the high costs. The retailer also found that the time it took to process returned products was longer than expected. The retailer worked with its suppliers to identify and address the causes of the delays.
By using performance metrics to control its reverse logistics program, the retailer was able to identify and address problems with the program. This helped the retailer to improve the efficiency and effectiveness of its reverse logistics program.
Controlling is an essential component of reverse logistics services. By monitoring the performance of their reverse logistics system and taking corrective action when necessary, businesses can improve the efficiency and effectiveness of their reverse logistics services. This can help businesses to reduce costs, improve customer satisfaction, and reduce their environmental impact.
4. Efficient
Efficiency is a critical component of reverse logistics services. It is the ability to manage the return of products, reduce waste, and recover value from end-of-life products in a way that is cost-effective and timely. Efficient reverse logistics services can help businesses to improve their bottom line and reduce their environmental impact.
There are a number of ways to improve the efficiency of reverse logistics services. One way is to use technology to automate tasks and track the progress of returned products. Another way is to work with suppliers and customers to develop a streamlined returns process. Finally, businesses can also invest in training their employees on the latest reverse logistics best practices.
Here is an example of how efficient reverse logistics services can benefit a business:
A large retailer implemented a new reverse logistics program to manage the return of its products. The program included a process for sorting the returned products, determining the best way to dispose of or recycle the products, and tracking the progress of the returned products. The retailer also worked with its suppliers to develop a process for returning the products to the suppliers.
The new reverse logistics program helped the retailer to reduce its costs by 15% and improve its customer satisfaction by 10%. The retailer was able to achieve these results by improving the efficiency of its reverse logistics process.
Efficient reverse logistics services are essential for businesses that want to reduce costs, improve customer satisfaction, and reduce their environmental impact. By taking the time to improve the efficiency of their reverse logistics services, businesses can gain a competitive advantage.
5. Cost-effective
In the context of reverse logistics services, cost-effectiveness refers to the ability to manage the return of products, reduce waste, and recover value from end-of-life products in a way that minimizes costs while still meeting customer needs. Cost-effective reverse logistics services are essential for businesses that want to improve their bottom line and reduce their environmental impact.
There are a number of ways to achieve cost-effective reverse logistics services. One way is to use technology to automate tasks and track the progress of returned products. This can help to reduce labor costs and improve efficiency. Another way to achieve cost-effective reverse logistics services is to work with suppliers and customers to develop a streamlined returns process. This can help to reduce the time and cost of processing returned products.
Here is an example of how cost-effective reverse logistics services can benefit a business:
A large retailer implemented a new reverse logistics program to manage the return of its products. The program included a process for sorting the returned products, determining the best way to dispose of or recycle the products, and tracking the progress of the returned products. The retailer also worked with its suppliers to develop a process for returning the products to the suppliers.
The new reverse logistics program helped the retailer to reduce its costs by 15% and improve its customer satisfaction by 10%. The retailer was able to achieve these results by improving the cost-effectiveness of its reverse logistics process.
Cost-effective reverse logistics services are essential for businesses that want to reduce costs, improve customer satisfaction, and reduce their environmental impact. By taking the time to improve the cost-effectiveness of their reverse logistics services, businesses can gain a competitive advantage.
6. Flow
In the context of reverse logistics services, flow refers to the efficient and effective movement of products, information, and resources throughout the reverse supply chain. It encompasses the processes involved in returning products from the point of consumption to the point of origin for the purpose of recapturing value or proper disposal.
- Planning and Coordination
Effective flow in reverse logistics services requires careful planning and coordination to ensure that products are returned in a timely and cost-efficient manner. This involves establishing clear communication channels between all parties involved in the reverse supply chain, including suppliers, manufacturers, distributors, and customers.
- Transportation and Logistics
The physical movement of products back through the supply chain is a critical aspect of flow in reverse logistics services. This involves selecting the most appropriate transportation methods and routes to minimize costs and transit times while ensuring the safe and secure delivery of returned products.
- Processing and Inspection
Once returned products arrive at the designated receiving facility, they must be processed and inspected to determine their condition and disposition. This may involve sorting, grading, testing, or refurbishing products to prepare them for resale, recycling, or disposal.
- Information Management
Effective flow in reverse logistics services requires the timely and accurate flow of information throughout the supply chain. This includes tracking the movement of returned products, managing inventory levels, and providing real-time updates to all stakeholders.
By optimizing the flow of products, information, and resources throughout the reverse supply chain, businesses can improve the efficiency and effectiveness of their reverse logistics services. This can lead to reduced costs, improved customer satisfaction, and a reduced environmental impact.
7. Raw materials
Raw materials play a critical role in the context of reverse logistics services, as they represent the starting point of the reverse supply chain and a valuable resource that can be recovered and reused.
- Definition and Importance
Raw materials are the basic components used in the production of goods and products. They can be sourced from a variety of sources, including mining, agriculture, and forestry. In the context of reverse logistics, raw materials are the materials that are recovered from end-of-life products and can be reused or recycled to create new products.
- Recovery and Recycling
One of the key goals of reverse logistics services is to recover and recycle raw materials from end-of-life products. This can be done through a variety of methods, such as disassembly, shredding, and chemical processing. Recovering and recycling raw materials can help to reduce the demand for virgin materials, which can lead to environmental benefits such as reduced pollution and greenhouse gas emissions.
- Remanufacturing and Refurbishment
In some cases, it is possible to remanufacture or refurbish end-of-life products instead of recycling them. Remanufacturing involves taking a used product and restoring it to its original condition or better. Refurbishment involves repairing or replacing damaged or worn components to restore a product to a usable condition. Remanufacturing and refurbishment can extend the lifespan of products and reduce the need for new raw materials.
- Environmental Impact
The use of reverse logistics services to recover and recycle raw materials can have a positive impact on the environment. By reducing the demand for virgin materials, reverse logistics services can help to conserve natural resources and reduce pollution. Additionally, recycling raw materials can help to reduce the amount of waste that is sent to landfills.
Overall, raw materials are an important aspect of reverse logistics services. By recovering and recycling raw materials, businesses can reduce costs, improve their environmental performance, and contribute to a more sustainable circular economy.
8. Finished goods
In the context of reverse logistics services, finished goods refer to products that have reached the end of their useful life or are no longer needed by the customer. These goods can be returned to the manufacturer or retailer for a variety of reasons, such as defects, obsolescence, or changes in consumer demand.
- Product Returns
One of the most common types of finished goods returned to manufacturers or retailers is product returns. Product returns can occur for a variety of reasons, such as customer dissatisfaction, defects, or changes in consumer demand. Reverse logistics services play a critical role in managing product returns by providing efficient and cost-effective ways to process and dispose of returned goods.
- End-of-Life Products
Another type of finished goods that is often managed by reverse logistics services is end-of-life products. End-of-life products are products that have reached the end of their useful life and are no longer needed by the customer. Reverse logistics services can help businesses to dispose of end-of-life products in a responsible and environmentally friendly manner.
- Excess Inventory
Excess inventory is another type of finished goods that can be managed by reverse logistics services. Excess inventory refers to products that are no longer needed by a business and are taking up valuable storage space. Reverse logistics services can help businesses to sell or dispose of excess inventory in a way that maximizes their return on investment.
- Recalls
In some cases, businesses may need to recall products that have been found to be defective or unsafe. Reverse logistics services can help businesses to manage product recalls by providing efficient and cost-effective ways to collect and dispose of recalled products.
Overall, finished goods play a critical role in the context of reverse logistics services. By providing efficient and cost-effective ways to manage product returns, end-of-life products, excess inventory, and recalls, reverse logistics services help businesses to reduce costs, improve customer satisfaction, and protect the environment.
9. Information
Information is a critical component of reverse logistics services. It enables businesses to track the movement of returned products, manage inventory levels, and make informed decisions about the disposition of returned goods. Effective information management can help businesses to improve the efficiency and cost-effectiveness of their reverse logistics operations.
There are a number of different types of information that are important for reverse logistics services. This includes:
- Product information: This includes information about the type of product, the manufacturer, the model number, and the serial number. This information is essential for tracking the movement of returned products and managing inventory levels.
- Customer information: This includes information about the customer who returned the product, such as their name, address, and contact information. This information is important for managing customer returns and providing customer service.
- Return information: This includes information about the reason for the return, the condition of the product, and the disposition of the product. This information is important for managing the reverse logistics process and making informed decisions about the disposition of returned goods.
Businesses can use a variety of different methods to collect and manage information for reverse logistics services. These methods include:
- Manual data entry: This involves manually entering information into a database or spreadsheet.
- Electronic data interchange (EDI): This involves exchanging information electronically with suppliers, manufacturers, and other trading partners.
- Radio frequency identification (RFID): This involves using RFID tags to track the movement of returned products.
The choice of information management method depends on a number of factors, such as the size of the business, the volume of returned products, and the available resources. Regardless of the method used, it is important to have a system in place for collecting, managing, and using information to improve the efficiency and effectiveness of reverse logistics services.
Frequently Asked Questions (FAQs) about Reverse Logistics Services
Reverse logistics services play a vital role in managing the return of products, reducing waste, and recovering value from end-of-life products. Here are some frequently asked questions about reverse logistics services:
Question 1: What are the benefits of using reverse logistics services?
Answer: Reverse logistics services offer a range of benefits, including reducing environmental impact through proper disposal and recycling, improving customer satisfaction through efficient returns processing, and reducing costs through the recovery of value from returned products.
Question 2: What types of products can be returned through reverse logistics services?
Answer: A wide range of products can be returned through reverse logistics services, including electronics, appliances, furniture, clothing, and hazardous materials.
Question 3: How do I choose a reverse logistics provider?
Answer: When choosing a reverse logistics provider, it is important to consider factors such as the provider’s experience, reputation, and ability to meet your specific needs.
Question 4: What are the costs associated with reverse logistics services?
Answer: The costs of reverse logistics services can vary depending on the type of product being returned, the volume of returns, and the distance the products need to be shipped.
Question 5: How can I improve the efficiency of my reverse logistics operations?
Answer: There are a number of ways to improve the efficiency of reverse logistics operations, such as using technology to automate tasks, establishing clear communication channels with suppliers and customers, and training employees on best practices.
Question 6: What are the environmental benefits of using reverse logistics services?
Answer: Reverse logistics services can help to reduce the environmental impact of businesses by reducing waste, recovering valuable materials, and promoting sustainable practices.
Overall, reverse logistics services are an essential part of any business’s supply chain. They can help businesses to reduce costs, improve customer satisfaction, and reduce their environmental impact.
Transition to the next article section:
For more information on reverse logistics services, please visit our website or contact us directly.
Tips for Effective Reverse Logistics Services
Reverse logistics services play a vital role in managing the return of products, reducing waste, and recovering value from end-of-life products. Here are some tips for businesses to improve the effectiveness of their reverse logistics operations:
Tip 1: Establish clear policies and procedures
Having clear policies and procedures in place for reverse logistics can help to streamline operations and improve efficiency. These policies and procedures should cover everything from product returns to end-of-life product disposal.
Tip 2: Use technology to automate tasks
Technology can be used to automate many tasks in the reverse logistics process, such as tracking product returns, managing inventory, and scheduling pickups. This can help to reduce labor costs and improve efficiency.
Tip 3: Work with a reputable reverse logistics provider
Partnering with a reputable reverse logistics provider can help to ensure that your reverse logistics operations are efficient and cost-effective. Look for a provider with experience in handling the type of products you need to return.
Tip 4: Train employees on best practices
Training employees on best practices for reverse logistics can help to improve the efficiency and accuracy of your operations. Employees should be trained on topics such as product handling, packaging, and shipping.
Tip 5: Monitor and evaluate your reverse logistics operations
Regularly monitoring and evaluating your reverse logistics operations can help to identify areas for improvement. Track metrics such as return rates, processing times, and costs to identify opportunities to improve efficiency and reduce costs.
Summary of key takeaways or benefits:
- Clear policies and procedures can streamline operations and improve efficiency.
- Technology can be used to automate tasks and reduce labor costs.
- Working with a reputable reverse logistics provider can ensure efficiency and cost-effectiveness.
- Training employees on best practices can improve the efficiency and accuracy of operations.
- Regularly monitoring and evaluating reverse logistics operations can help to identify areas for improvement.
By following these tips, businesses can improve the effectiveness of their reverse logistics services and gain a competitive advantage.
Transition to the article’s conclusion:
Reverse logistics services are an essential part of any business’s supply chain. By effectively managing reverse logistics operations, businesses can reduce costs, improve customer satisfaction, and reduce their environmental impact.
Conclusion
Reverse logistics services play a crucial role in reducing waste, recovering value from end-of-life products, and improving customer satisfaction. Through effective planning, implementation, and control, businesses can optimize their reverse logistics operations to gain a competitive advantage.
As environmental concerns continue to grow, reverse logistics services will become increasingly important for businesses that want to reduce their environmental impact. By embracing sustainable practices and investing in reverse logistics, businesses can contribute to a more circular economy and create a more sustainable future.