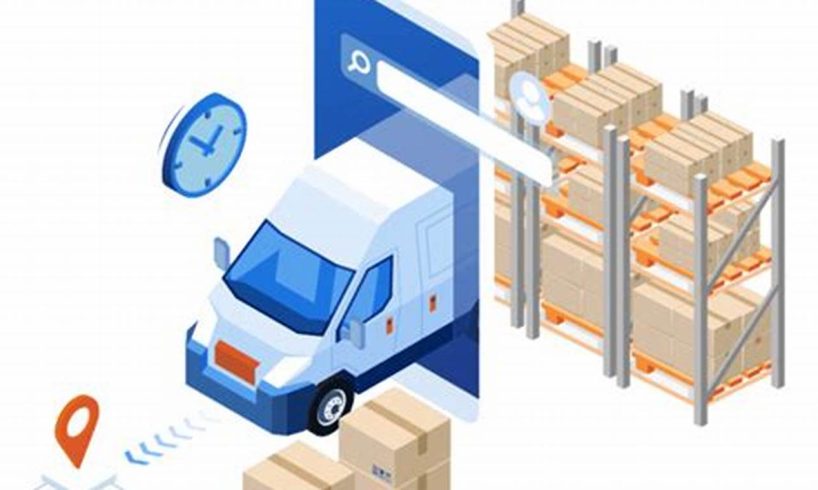
Service parts logistics is the process of managing the flow of service parts from the supplier to the customer. It involves planning, organizing, and controlling the movement and storage of service parts to ensure that they are available when and where they are needed. Service parts logistics is a critical part of any organization’s supply chain, as it can help to improve customer satisfaction, reduce costs, and increase efficiency.
There are many benefits to effective service parts logistics, including:
- Improved customer satisfaction: When service parts are available when and where they are needed, customers are more likely to be satisfied with the service they receive.
- Reduced costs: Effective service parts logistics can help to reduce costs by optimizing inventory levels and reducing the need for expedited shipping.
- Increased efficiency: A well-managed service parts logistics system can help to improve efficiency by streamlining the flow of parts from the supplier to the customer.
Service parts logistics is a complex and challenging process, but it is essential for any organization that wants to provide excellent customer service. By understanding the importance of service parts logistics and implementing effective strategies, organizations can improve customer satisfaction, reduce costs, and increase efficiency.
1. Planning
Planning is a critical part of service parts logistics. It involves forecasting demand for service parts, determining inventory levels, and establishing transportation routes. This planning process helps to ensure that service parts are available when and where they are needed.
- Forecasting demand for service parts: This involves using historical data, market research, and other factors to forecast demand for service parts. Accurate demand forecasting is essential for ensuring that there are enough parts to meet demand without overstocking.
- Determining inventory levels: This involves setting inventory levels for service parts. Inventory levels should be high enough to meet demand, but not so high that there is excess inventory. Excess inventory can tie up capital and lead to obsolescence.
- Establishing transportation routes: This involves selecting and managing transportation carriers to ensure that parts are delivered on time and in good condition. Transportation routes should be efficient and cost-effective.
By effectively planning for service parts logistics, organizations can improve customer satisfaction, reduce costs, and increase efficiency.
2. Organizing
Organizing is a critical part of service parts logistics. It involves setting up systems and processes for managing service parts inventory, including receiving, storing, and shipping parts. This organization process helps to ensure that service parts are available when and where they are needed.
- Inventory management: This involves managing inventory levels to ensure that there are enough parts to meet demand without overstocking. Inventory management systems help to track inventory levels, reorder parts when necessary, and manage returns.
- Warehouse management: This involves managing the physical storage of service parts. Warehouse management systems help to track the location of parts, optimize storage space, and manage the movement of parts in and out of the warehouse.
- Shipping management: This involves managing the shipping of service parts to customers. Shipping management systems help to select and manage transportation carriers, track shipments, and manage returns.
- Customer service: This involves providing excellent customer service to ensure that customers receive the parts they need when they need them. Customer service representatives can help customers track shipments, resolve problems, and return parts.
By effectively organizing service parts inventory, organizations can improve customer satisfaction, reduce costs, and increase efficiency.
3. Controlling
Controlling is a critical part of service parts logistics. It involves monitoring service parts inventory levels, tracking shipments, and managing returns. This controlling process helps to ensure that service parts are available when and where they are needed.
Monitoring service parts inventory levels is essential for ensuring that there are enough parts to meet demand without overstocking. Inventory levels should be monitored regularly and adjusted as needed. Tracking shipments is important for memastikan that parts are delivered on time and in good condition. Shipments should be tracked from the time they leave the warehouse until they are delivered to the customer.
Managing returns is important for ensuring that customers are satisfied with the service they receive. Returns should be processed quickly and efficiently. Customers should be kept informed of the status of their return and should be given a refund or replacement as soon as possible.
By effectively controlling service parts inventory, organizations can improve customer satisfaction, reduce costs, and increase efficiency.
4. Inventory management
Inventory management is a critical part of service parts logistics. It involves optimizing inventory levels to ensure that there are enough parts to meet demand without overstocking. Overstocking can lead to excess inventory, which can tie up capital and lead to obsolescence. Understocking can lead to stockouts, which can result in lost sales and dissatisfied customers.
- Safety stock: Safety stock is a buffer of inventory that is held to protect against unexpected increases in demand or disruptions in the supply chain. Safety stock levels should be set based on the criticality of the part, the lead time for replenishment, and the cost of holding inventory.
- Reorder point: The reorder point is the inventory level at which a new order is placed. The reorder point should be set based on the safety stock level, the lead time for replenishment, and the expected demand during the lead time.
- Inventory turnover: Inventory turnover is a measure of how quickly inventory is sold and replaced. A high inventory turnover rate indicates that inventory is being managed efficiently. A low inventory turnover rate indicates that inventory is not being sold quickly enough and may be at risk of obsolescence.
- Inventory accuracy: Inventory accuracy is the degree to which the physical inventory matches the records. Inaccurate inventory can lead to stockouts, overstocking, and lost sales. Inventory accuracy can be improved through regular cycle counting and the use of inventory management software.
By effectively managing inventory, organizations can improve customer satisfaction, reduce costs, and increase efficiency.
5. Transportation
Transportation is a critical component of service parts logistics. It ensures that service parts are delivered to the right place, at the right time, and in good condition. Without effective transportation, service parts logistics would not be able to function efficiently.
There are a number of factors to consider when selecting and managing transportation carriers for service parts logistics. These factors include:
- Reliability: The transportation carrier must be reliable and able to deliver parts on time and in good condition.
- Cost: The transportation carrier must be cost-effective.
- Flexibility: The transportation carrier must be able to adapt to changes in demand and delivery schedules.
- Technology: The transportation carrier must have the technology to track shipments and provide real-time updates.
By carefully considering these factors, organizations can select and manage transportation carriers that meet their specific service parts logistics needs. Effective transportation management can help organizations improve customer satisfaction, reduce costs, and increase efficiency.
Here are some real-life examples of how effective transportation management has benefited organizations:
- A manufacturing company was able to reduce its delivery time by 25% by partnering with a transportation carrier that specialized in expedited shipping.
- A retail company was able to reduce its transportation costs by 15% by negotiating volume discounts with its transportation carriers.
- A healthcare provider was able to improve patient satisfaction by partnering with a transportation carrier that provided real-time tracking of shipments.
These examples illustrate the practical significance of effective transportation management in service parts logistics. By understanding the connection between transportation and service parts logistics, organizations can improve their overall supply chain performance.
6. Customer service
Excellent customer service is essential for any business, but it is especially important in service parts logistics. When customers need service parts, they need them quickly and efficiently. A good customer service team can help to ensure that customers get the parts they need, when they need them, and at a fair price.
- Responsiveness: A good customer service team is responsive to customer inquiries. They should be able to answer questions quickly and accurately, and they should be able to resolve problems quickly and efficiently.
- Knowledge: A good customer service team is knowledgeable about the products and services that they sell. They should be able to answer questions about product availability, pricing, and delivery times.
- Courtesy: A good customer service team is courteous and professional. They should be able to handle customer inquiries in a friendly and helpful manner.
- Problem-solving skills: A good customer service team has good problem-solving skills. They should be able to identify and resolve customer problems quickly and efficiently.
By providing excellent customer service, businesses can improve customer satisfaction, increase sales, and build long-term relationships with their customers.
7. Technology
Technology plays an increasingly important role in service parts logistics. By using technology, businesses can improve the efficiency and effectiveness of their service parts logistics operations. This can lead to improved customer service, reduced costs, and increased profitability.
- Real-time tracking
Real-time tracking technology allows businesses to track the location of their service parts in real time. This can help to improve customer service by providing customers with accurate delivery times. It can also help to reduce costs by reducing the need for expedited shipping. - Automated inventory management
Automated inventory management systems can help businesses to manage their inventory more efficiently. These systems can track inventory levels, generate purchase orders, and manage returns. This can help to reduce costs and improve customer service by ensuring that businesses have the right parts in stock when they need them. - Predictive analytics
Predictive analytics can help businesses to predict demand for service parts. This information can be used to optimize inventory levels and improve customer service by ensuring that businesses have the right parts in stock when they need them. - Mobile technology
Mobile technology can help businesses to improve the efficiency and effectiveness of their service parts logistics operations. Mobile devices can be used to track inventory, manage orders, and communicate with customers. This can help to improve customer service and reduce costs.
These are just a few of the ways that technology can be used to improve service parts logistics. By using technology, businesses can improve customer service, reduce costs, and increase profitability.
8. Metrics
Metrics are essential for measuring the performance of service parts logistics. By tracking key metrics, businesses can identify areas for improvement and make data-driven decisions to improve the efficiency and effectiveness of their service parts logistics operations.
Some of the key metrics that businesses should track include:
- Inventory turnover: This metric measures how quickly inventory is sold and replaced. A high inventory turnover rate indicates that inventory is being managed efficiently. A low inventory turnover rate indicates that inventory is not being sold quickly enough and may be at risk of obsolescence.
- Fill rate: This metric measures the percentage of customer orders that are filled from inventory. A high fill rate indicates that the business has the right parts in stock to meet customer demand. A low fill rate indicates that the business is experiencing stockouts, which can lead to lost sales and dissatisfied customers.
- Delivery time: This metric measures the time it takes for parts to be delivered to customers. A short delivery time indicates that the business is able to meet customer demand quickly and efficiently. A long delivery time can lead to customer dissatisfaction and lost sales.
- Customer satisfaction: This metric measures the level of satisfaction that customers have with the service parts logistics operation. A high customer satisfaction rating indicates that the business is meeting customer needs and expectations. A low customer satisfaction rating indicates that the business needs to improve its service parts logistics operation.
By tracking these key metrics, businesses can gain valuable insights into the performance of their service parts logistics operations. This information can be used to identify areas for improvement and make data-driven decisions to improve the efficiency and effectiveness of the operation.
For example, a business that is experiencing a low fill rate may need to increase its inventory levels or improve its forecasting accuracy. A business that is experiencing a long delivery time may need to improve its shipping process or partner with a different transportation carrier. By tracking key metrics and taking corrective action, businesses can improve the performance of their service parts logistics operations and gain a competitive advantage.
9. Continuous improvement
Continuous improvement is a key component of service parts logistics. It involves regularly reviewing and improving service parts logistics processes to identify and eliminate waste, reduce costs, and improve customer satisfaction. Continuous improvement can be applied to all aspects of service parts logistics, from inventory management to transportation to customer service.
There are many benefits to continuous improvement in service parts logistics. Some of the benefits include:
- Reduced costs: Continuous improvement can help to reduce costs by identifying and eliminating waste in service parts logistics processes. For example, a company may be able to reduce inventory costs by implementing a just-in-time inventory system.
- Improved customer satisfaction: Continuous improvement can help to improve customer satisfaction by reducing the time it takes to deliver parts and by improving the accuracy of orders. For example, a company may be able to improve customer satisfaction by implementing a real-time tracking system to track the location of parts.
- Increased efficiency: Continuous improvement can help to increase efficiency by streamlining service parts logistics processes. For example, a company may be able to reduce the time it takes to process orders by implementing an automated order processing system.
Continuous improvement is an ongoing process. It is important to regularly review service parts logistics processes and identify areas for improvement. By making small, incremental improvements over time, businesses can significantly improve the efficiency and effectiveness of their service parts logistics operations.
Here are some examples of continuous improvement in service parts logistics:
- A company implemented a just-in-time inventory system to reduce inventory costs.
- A company implemented a real-time tracking system to track the location of parts and improve customer satisfaction.
- A company implemented an automated order processing system to reduce the time it takes to process orders.
These are just a few examples of how continuous improvement can be applied to service parts logistics. By continuously improving service parts logistics processes, businesses can reduce costs, improve customer satisfaction, and increase efficiency.
FAQs on Service Parts Logistics
Service parts logistics is a critical part of any organization’s supply chain. It involves the planning, organizing, and controlling of the movement and storage of service parts to ensure that they are available when and where they are needed. Effective service parts logistics can help to improve customer satisfaction, reduce costs, and increase efficiency.
Question 1: What are the benefits of effective service parts logistics?
Answer: Effective service parts logistics can provide numerous benefits, including improved customer satisfaction, reduced costs, and increased efficiency.
Question 2: What are the key aspects of service parts logistics?
Answer: The key aspects of service parts logistics include planning, organizing, controlling, inventory management, transportation, customer service, technology, metrics, and continuous improvement.
Question 3: How can technology improve service parts logistics?
Answer: Technology can improve service parts logistics in several ways, such as enabling real-time tracking, automating inventory management, providing predictive analytics, and facilitating mobile access.
Question 4: Why is continuous improvement important in service parts logistics?
Answer: Continuous improvement is crucial in service parts logistics as it allows organizations to regularly review and enhance their processes, leading to reduced costs, improved customer satisfaction, and increased efficiency.
Question 5: What are some examples of continuous improvement in service parts logistics?
Answer: Examples of continuous improvement in service parts logistics include implementing just-in-time inventory systems, real-time tracking systems, and automated order processing systems.
Question 6: How can organizations measure the performance of their service parts logistics operations?
Answer: Organizations can measure the performance of their service parts logistics operations by tracking key metrics such as inventory turnover, fill rate, delivery time, and customer satisfaction.
Summary: Effective service parts logistics is essential for organizations to meet customer demand, optimize inventory, reduce costs, and enhance overall supply chain efficiency. By understanding the key aspects, benefits, and continuous improvement principles of service parts logistics, organizations can establish robust and responsive systems that support their business objectives.
Transition to the next article section: Explore the intricate world of service parts logistics further by delving into specific case studies and industry best practices.
Service Parts Logistics Tips
Effective service parts logistics is essential for maintaining operational efficiency and customer satisfaction. Here are some valuable tips to enhance your service parts logistics operations:
Tip 1: Implement a Robust Inventory Management System
Establish a centralized inventory management system that provides real-time visibility into stock levels, order status, and demand patterns. Utilize inventory optimization techniques such as ABC analysis and safety stock management to ensure optimal inventory levels.
Tip 2: Optimize Transportation and Logistics
Partner with reliable transportation providers and optimize shipping routes to reduce delivery times and costs. Consider implementing just-in-time delivery systems or vendor-managed inventory programs to streamline the flow of parts.
Tip 3: Leverage Technology for Automation
Automate repetitive tasks such as order processing, inventory tracking, and shipment monitoring. Utilize technology solutions like radio frequency identification (RFID) or barcode scanning for efficient and accurate data capture.
Tip 4: Focus on Continuous Improvement
Regularly review and assess your service parts logistics processes to identify areas for improvement. Implement lean principles and Six Sigma methodologies to eliminate waste, improve efficiency, and enhance customer satisfaction.
Tip 5: Foster Collaboration and Communication
Establish clear communication channels between different departments, including sales, operations, and customer service. Foster collaboration to ensure that all stakeholders are aligned on service parts availability, lead times, and customer expectations.
Tip 6: Invest in Training and Development
Provide comprehensive training to your service parts logistics team to ensure they have the necessary knowledge and skills. Regular training sessions on inventory management, transportation optimization, and customer service best practices can enhance their performance.
Tip 7: Monitor Key Performance Indicators (KPIs)
Establish and track relevant KPIs to measure the effectiveness of your service parts logistics operations. Monitor metrics such as inventory turnover, fill rates, delivery times, and customer satisfaction scores to identify areas for improvement and make data-driven decisions.
Tip 8: Seek Professional Advice
Consider consulting with experienced service parts logistics professionals or industry experts to gain valuable insights and best practices. They can provide tailored guidance and support to help you optimize your operations and achieve your business goals.
By implementing these tips, organizations can significantly improve their service parts logistics operations, leading to enhanced customer service, reduced costs, and increased efficiency.
Transition to the article’s conclusion: Effective service parts logistics is a continuous journey of improvement. By embracing these tips and fostering a culture of excellence, organizations can establish a robust and responsive service parts logistics system that supports their overall business success.
Conclusion
Service parts logistics plays a critical role in ensuring the smooth functioning of various industries, enabling businesses to meet customer demands efficiently and effectively. Throughout this article, we explored key aspects of service parts logistics, including planning, inventory management, transportation, customer service, and continuous improvement.
Effective service parts logistics not only enhances customer satisfaction but also optimizes inventory levels, reduces operational costs, and improves overall supply chain performance. By understanding and implementing best practices, organizations can establish a robust service parts logistics system that supports their long-term growth and success. As technology continues to advance and customer expectations evolve, it is essential for organizations to embrace innovation and continuously improve their service parts logistics operations to maintain a competitive edge and deliver exceptional service.