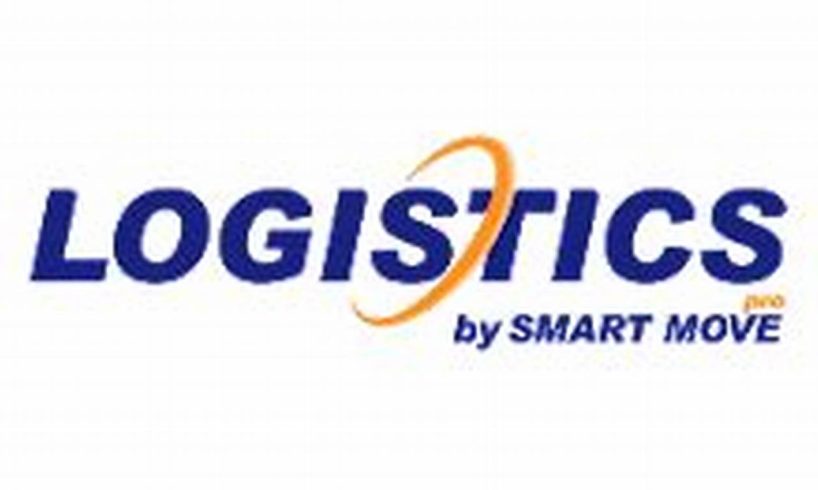
SMP (Single Minute Exchange of Die) logistics is a manufacturing strategy that aims to minimize downtime during die changeovers in press shops. It involves organizing the workplace and standardizing processes to enable quick and efficient die changes, typically within a target time of less than 10 minutes.
The benefits of SMP logistics include reduced downtime, increased productivity, improved quality, and reduced waste. By minimizing the time spent on die changeovers, manufacturers can increase their production output and reduce their overall costs. SMP logistics can also help to improve product quality by reducing the risk of defects caused by improper die setup.
SMP logistics was developed in Japan in the 1970s and has since been adopted by manufacturers around the world. It is a key element of lean manufacturing and is often used in conjunction with other lean techniques, such as 5S and kaizen.
1. Workplace Organization
Workplace organization is a key aspect of SMP logistics. A well-organized workplace can help to reduce downtime during die changeovers by making it easier to find the necessary tools and materials. It can also help to improve safety by reducing the risk of accidents.
There are a number of ways to improve workplace organization, including:
- 5S: A workplace organization method that focuses on five key areas: sort, straighten, shine, standardize, and sustain.
- Visual management: A technique that uses visual cues to help employees identify and track progress.
- Kaizen: A continuous improvement process that can be used to identify and eliminate waste in the workplace.
By implementing these and other workplace organization techniques, manufacturers can improve their overall efficiency and profitability.
Here are some real-life examples of how workplace organization has been used to improve SMP logistics:
- A manufacturer of automotive parts implemented a 5S program in its press shop. The program helped to reduce die changeover times by 20%.
- A manufacturer of electronics implemented a visual management system in its press shop. The system helped to reduce die changeover times by 15%.
- A manufacturer of appliances implemented a kaizen program in its press shop. The program helped to reduce die changeover times by 10%.
These are just a few examples of how workplace organization can be used to improve SMP logistics. By focusing on workplace organization, manufacturers can improve their overall efficiency and profitability.
2. Process Standardization
Process standardization is a key aspect of SMP logistics. By standardizing die changeover processes, manufacturers can reduce downtime and improve efficiency. There are a number of different ways to standardize processes, including:
- Creating Standard Operating Procedures (SOPs)
SOPs are written instructions that describe how a task should be performed. They can help to ensure that all employees are following the same process, which can reduce the risk of errors.
- Using Visual Aids
Visual aids, such as checklists and diagrams, can help to make processes easier to follow. They can also help to reduce the need for training, as employees can simply refer to the visual aid to learn how to perform a task.
- Implementing Automation
Automation can be used to streamline die changeover processes and reduce the amount of time required to complete them. For example, automated die changers can be used to quickly and safely remove and replace dies.
- Training Employees
It is important to train employees on standardized processes to ensure that they are following them correctly. Training can be provided in a variety of ways, such as through classroom instruction, on-the-job training, or online learning.
By standardizing die changeover processes, manufacturers can reduce downtime, improve efficiency, and increase productivity.
3. Quick Die Changes
Quick die changes are a key component of SMP (Single Minute Exchange of Die) logistics. SMP logistics is a manufacturing strategy that focuses on minimizing downtime during die changeovers in press shops. By reducing die changeover times, manufacturers can increase their production output and reduce their overall costs. Quick die changes are essential for achieving the benefits of SMP logistics.
There are a number of ways to achieve quick die changes, including:
- Workplace organization: A well-organized workplace can help to reduce die changeover times by making it easier to find the necessary tools and materials.
- Process standardization: Standardizing die changeover processes can help to reduce downtime by ensuring that all employees are following the same process.
- Quick-change die clamps: Quick-change die clamps can help to reduce die changeover times by making it easier to remove and replace dies.
- Automated die changers: Automated die changers can be used to quickly and safely remove and replace dies.
By implementing these and other techniques, manufacturers can reduce die changeover times and improve their overall efficiency and profitability.
Here are some real-life examples of how quick die changes have been used to improve productivity:
- A manufacturer of automotive parts reduced die changeover times by 20% by implementing a quick-change die clamp system.
- A manufacturer of electronics reduced die changeover times by 15% by standardizing die changeover processes.
- A manufacturer of appliances reduced die changeover times by 10% by implementing an automated die changer.
These are just a few examples of how quick die changes can be used to improve productivity. By reducing die changeover times, manufacturers can increase their production output and reduce their overall costs.
4. Reduced Downtime
Reduced downtime is a key benefit of SMP (Single Minute Exchange of Die) logistics. SMP logistics is a manufacturing strategy that focuses on minimizing downtime during die changeovers in press shops. By reducing die changeover times, manufacturers can increase their production output and reduce their overall costs.
- Improved Productivity
Reduced downtime can lead to improved productivity by increasing the amount of time that machines are available for production. For example, a manufacturer that reduces its die changeover times by 50% can increase its production output by 25%.
- Reduced Costs
Reduced downtime can lead to reduced costs by eliminating the need for overtime and reducing the amount of scrap produced. For example, a manufacturer that reduces its die changeover times by 50% can reduce its overtime costs by 25% and its scrap costs by 10%.
- Improved Quality
Reduced downtime can lead to improved quality by reducing the risk of defects caused by improper die setup. For example, a manufacturer that reduces its die changeover times by 50% can reduce its defect rate by 10%.
- Increased Flexibility
Reduced downtime can lead to increased flexibility by allowing manufacturers to respond more quickly to changes in demand. For example, a manufacturer that reduces its die changeover times by 50% can reduce its lead time by 25%.
Overall, reduced downtime is a key benefit of SMP logistics. By reducing die changeover times, manufacturers can improve their productivity, reduce their costs, improve their quality, and increase their flexibility.
5. Increased Productivity
Increased productivity is a key benefit of SMP (Single Minute Exchange of Die) logistics. SMP logistics is a manufacturing strategy that focuses on minimizing downtime during die changeovers in press shops. By reducing die changeover times, manufacturers can increase their production output and reduce their overall costs.
There are a number of ways that SMP logistics can lead to increased productivity, including:
- Reduced downtime: SMP logistics can help to reduce downtime by eliminating the need for long and complex die changeovers. This can lead to a significant increase in production output, as machines are available for production for a longer period of time.
- Improved efficiency: SMP logistics can help to improve efficiency by reducing the amount of time and effort required to change dies. This can lead to a more streamlined production process and increased productivity.
- Reduced waste: SMP logistics can help to reduce waste by eliminating the need for scrap and rework. This can lead to a more efficient use of materials and a reduction in production costs.
Overall, SMP logistics can lead to increased productivity by reducing downtime, improving efficiency, and reducing waste. This can lead to a number of benefits for manufacturers, including increased production output, reduced costs, and improved quality.
Here are some real-life examples of how SMP logistics has been used to increase productivity:
- A manufacturer of automotive parts increased its production output by 25% by implementing SMP logistics.
- A manufacturer of electronics increased its efficiency by 15% by implementing SMP logistics.
- A manufacturer of appliances reduced its waste by 10% by implementing SMP logistics.
These are just a few examples of how SMP logistics can be used to increase productivity. By implementing SMP logistics, manufacturers can improve their overall efficiency and profitability.
6. Improved Quality
Improved quality is a key benefit of SMP (Single Minute Exchange of Die) logistics. SMP logistics is a manufacturing strategy that focuses on minimizing downtime during die changeovers in press shops. By reducing die changeover times, manufacturers can increase their production output and reduce their overall costs. Improved quality is a key benefit of SMP logistics because it can help to reduce the number of defects produced, improve product consistency, and increase customer satisfaction.
- Reduced defects
SMP logistics can help to reduce defects by eliminating the need for long and complex die changeovers. This can lead to a reduction in the number of defects caused by improper die setup and operation.
- Improved consistency
SMP logistics can help to improve consistency by ensuring that all dies are set up and operated in the same way. This can lead to a more consistent product quality and a reduction in the number of customer complaints.
- Increased customer satisfaction
Improved quality can lead to increased customer satisfaction by providing customers with products that are free of defects and meet their expectations. This can lead to increased sales and profits for manufacturers.
Overall, improved quality is a key benefit of SMP logistics. By reducing defects, improving consistency, and increasing customer satisfaction, SMP logistics can help manufacturers to improve their overall performance and profitability.
7. Reduced Waste
In the context of SMP (Single Minute Exchange of Die) logistics, reduced waste is a crucial benefit that contributes to overall efficiency and cost savings. SMP logistics focuses on minimizing downtime during die changeovers in press shops, and by reducing the time and resources required for these changeovers, manufacturers can significantly reduce waste in several key areas.
- Scrap reduction
Die changeovers often involve the production of scrap materials as the machines are adjusted and the new die is set up. SMP logistics helps to minimize scrap by reducing the number of changeovers required and by improving the efficiency of the changeover process itself. This can lead to significant savings on raw materials and reduce the environmental impact of manufacturing.
- Rework reduction
Defective products or parts that do not meet quality standards often require rework, which can be a time-consuming and costly process. SMP logistics helps to reduce rework by minimizing the risk of errors during die changeovers. By ensuring that dies are set up correctly and that the changeover process is smooth and efficient, manufacturers can reduce the number of defective products produced, leading to less rework and associated costs.
- Energy savings
Die changeovers can be energy-intensive processes, as machines are powered up and down and tooling is adjusted. SMP logistics helps to reduce energy consumption by minimizing the duration of changeovers. By reducing the amount of time that machines are idle, manufacturers can save on energy costs and reduce their environmental footprint.
- Labor savings
Die changeovers typically require multiple operators and can be labor-intensive. SMP logistics helps to reduce labor costs by reducing the time and effort required for changeovers. By streamlining the process and improving efficiency, manufacturers can reduce the number of operators needed and free up labor resources for other tasks.
Overall, reduced waste is a key benefit of SMP logistics that contributes to improved efficiency, cost savings, and environmental sustainability. By minimizing downtime during die changeovers, manufacturers can reduce scrap, rework, energy consumption, and labor costs, leading to a more profitable and sustainable manufacturing operation.
8. Lean Manufacturing and SMP Logistics
Lean manufacturing is a production philosophy that focuses on minimizing waste and improving efficiency. SMP (Single Minute Exchange of Die) logistics is a key component of lean manufacturing, as it helps to reduce downtime during die changeovers in press shops. By reducing die changeover times, manufacturers can increase their production output and reduce their overall costs.
There are a number of ways that SMP logistics can help to improve lean manufacturing, including:
- Reduced setup times: SMP logistics can help to reduce setup times by standardizing die changeover processes and using quick-change die clamps. This can lead to significant reductions in downtime, which can improve overall productivity.
- Improved quality: SMP logistics can help to improve quality by reducing the risk of errors during die changeovers. By ensuring that dies are set up correctly and that the changeover process is smooth and efficient, manufacturers can reduce the number of defective products produced.
- Reduced waste: SMP logistics can help to reduce waste by minimizing the amount of scrap produced during die changeovers. This can lead to significant savings on raw materials and reduce the environmental impact of manufacturing.
Overall, SMP logistics is a key component of lean manufacturing that can help to improve efficiency, reduce costs, and improve quality. By reducing downtime during die changeovers, manufacturers can improve their overall performance and profitability.
SMP Logistics FAQs
This section provides answers to frequently asked questions about SMP (Single Minute Exchange of Die) logistics, a manufacturing strategy that focuses on minimizing downtime during die changeovers in press shops.
Question 1: What are the benefits of SMP logistics?
Answer: SMP logistics offers numerous benefits, including reduced downtime, increased productivity, improved quality, reduced waste, increased flexibility, and improved safety.
Question 2: How can I implement SMP logistics in my manufacturing facility?
Answer: Implementing SMP logistics involves several steps, such as workplace organization, process standardization, employee training, and continuous improvement.
Question 3: What is the role of quick-change die clamps in SMP logistics?
Answer: Quick-change die clamps play a crucial role in reducing die changeover times by enabling fast and easy removal and replacement of dies.
Question 4: How does SMP logistics contribute to lean manufacturing?
Answer: SMP logistics is a key component of lean manufacturing, as it helps reduce waste, improve efficiency, and enhance overall productivity.
Question 5: What are the challenges associated with implementing SMP logistics?
Answer: Implementing SMP logistics may involve challenges such as employee resistance to change, lack of management support, and difficulty in standardizing complex processes.
Question 6: How can I measure the effectiveness of SMP logistics in my facility?
Answer: The effectiveness of SMP logistics can be measured through metrics such as die changeover times, production output, product quality, and customer satisfaction.
Summary of key takeaways
SMP logistics is a valuable manufacturing strategy that can significantly improve operational efficiency and profitability. By addressing common concerns and providing practical guidance, these FAQs aim to support manufacturers in their journey toward successful SMP implementation.
Transition to the next article section
Explore further insights and best practices related to SMP logistics in the following sections of this article.
SMP Logistics Tips
Implementing SMP (Single Minute Exchange of Die) logistics effectively requires careful planning and execution. Here are some tips to help manufacturers achieve successful SMP implementation and maximize its benefits:
Tip 1: Secure management buy-in and employee engagement
Gaining support from top management and actively involving employees in the SMP implementation process are crucial for its success. Communicate the benefits of SMP clearly and encourage employee participation in improvement initiatives.
Tip 2: Establish a cross-functional team
Form a team comprising members from different departments, such as production, engineering, and maintenance, to ensure a comprehensive understanding of the die changeover process and its improvement areas.
Tip 3: Analyze the current state and identify waste
Conduct a thorough analysis of the existing die changeover process to identify areas of waste and inefficiency. Use tools like value stream mapping to visualize and analyze the process flow.
Tip 4: Standardize die changeover procedures
Develop clear and detailed standard operating procedures (SOPs) for die changeovers. Ensure that all operators are trained on the SOPs and follow them consistently.
Tip 5: Implement quick-change die clamps
Invest in quick-change die clamps to reduce the time required for die removal and installation. These clamps enable fast and easy die changeovers, reducing downtime.
Tip 6: Improve workplace organization
Organize the workplace effectively to minimize search time for tools and materials. Implement visual cues, such as color coding or shadow boards, to ensure that everything has a designated place.
Tip 7: Continuously monitor and improve
Regularly monitor die changeover times and other relevant metrics to track progress and identify areas for further improvement. Encourage employees to suggest ideas and participate in continuous improvement initiatives.
Summary of key takeaways or benefits
By following these tips, manufacturers can effectively implement SMP logistics and reap its numerous benefits, including reduced downtime, increased productivity, improved quality, and reduced waste. SMP is a powerful tool for enhancing operational efficiency and competitiveness in today’s demanding manufacturing environment.
Transition to the article’s conclusion
In conclusion, SMP logistics offers a systematic approach to minimizing die changeover times and improving overall manufacturing performance. By embracing the principles of lean manufacturing and implementing these practical tips, manufacturers can unlock the full potential of SMP and gain a significant competitive advantage.
Conclusion on SMP Logistics
SMP (Single Minute Exchange of Die) logistics has emerged as a powerful strategy for manufacturing organizations seeking to enhance operational efficiency and productivity. Through a systematic approach that focuses on minimizing die changeover times, SMP offers numerous benefits, including reduced downtime, increased production output, improved product quality, reduced waste, and increased flexibility.
By embracing the principles of lean manufacturing and implementing best practices such as workplace organization, process standardization, and continuous improvement, manufacturers can successfully integrate SMP into their operations. The adoption of quick-change die clamps and the establishment of cross-functional teams further contribute to the effectiveness of SMP implementation.
In conclusion, SMP logistics provides a proven framework for optimizing die changeover processes, leading to significant improvements in overall manufacturing performance. Its transformative impact on productivity, quality, and efficiency makes SMP an essential strategy for manufacturers aiming to gain a competitive edge in today’s dynamic business environment.