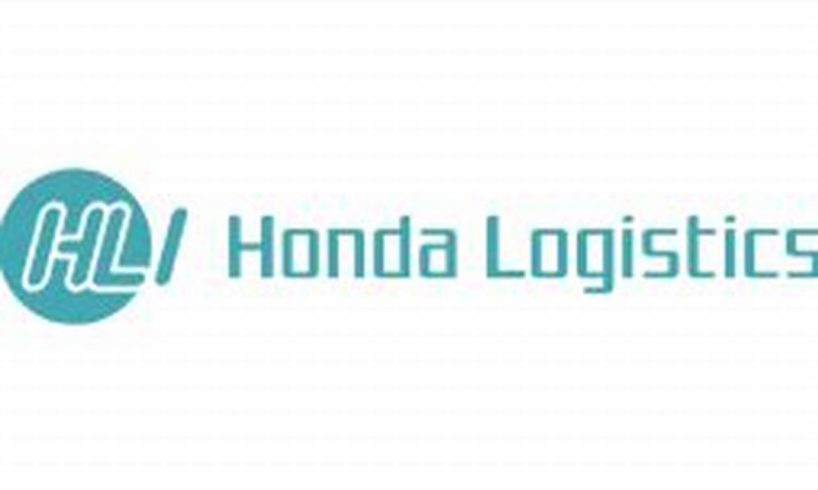
Honda Logistics North America, Inc. is a subsidiary of Honda Motor Company, Ltd. that provides logistics services to Honda’s manufacturing plants in North America. The company was founded in 1998 and is headquartered in Marysville, Ohio. Honda Logistics North America, Inc. operates a network of distribution centers and transportation providers to manage the flow of parts and materials to Honda’s assembly plants. The company also provides logistics services to Honda’s sales and marketing operations in North America.
Honda Logistics North America, Inc. plays a vital role in Honda’s manufacturing and sales operations in North America. The company’s efficient and reliable logistics services help to ensure that Honda’s plants have the parts and materials they need to produce vehicles, and that Honda’s sales and marketing operations have the products they need to meet customer demand.
Honda Logistics North America, Inc. is a key part of Honda’s success in North America. The company’s commitment to providing high-quality logistics services has helped Honda to become one of the leading automakers in the region.
1. Logistics provider
Honda Logistics North America, Inc. (HLNA) is a vital component of Honda’s North American operations, providing comprehensive logistics services to the company’s manufacturing plants in the region. This includes managing the flow of parts and materials to Honda’s assembly plants, as well as providing logistics services to Honda’s sales and marketing operations in North America.
HLNA plays a critical role in ensuring that Honda’s manufacturing plants have the parts and materials they need to produce vehicles, and that Honda’s sales and marketing operations have the products they need to meet customer demand. The company’s efficient and reliable logistics services help to minimize production disruptions and ensure that Honda can meet its customer commitments.
HLNA’s expertise in logistics management is a key competitive advantage for Honda. The company’s ability to manage the complex flow of parts and materials to Honda’s manufacturing plants helps to reduce costs and improve efficiency. HLNA’s commitment to quality and customer service also helps to ensure that Honda’s products are delivered to customers on time and in good condition.
In conclusion, HLNA’s role as a logistics provider is essential to Honda’s success in North America. The company’s expertise in logistics management helps to ensure that Honda’s manufacturing plants have the parts and materials they need to produce vehicles, and that Honda’s sales and marketing operations have the products they need to meet customer demand.
2. Distribution network
Honda Logistics North America, Inc. (HLNA) operates a vast network of distribution centers to manage the flow of parts and materials to Honda’s manufacturing plants in North America. This network is essential to HLNA’s ability to provide comprehensive logistics services to Honda’s manufacturing and sales operations.
- Efficient inventory management
HLNA’s distribution centers are strategically located to minimize transportation costs and delivery times. The company also uses advanced inventory management systems to optimize stock levels and ensure that the right parts are available at the right time.
- Quality control
HLNA’s distribution centers are equipped with state-of-the-art quality control to ensure that all parts and materials meet Honda’s high standards. This helps to prevent production disruptions and ensures that Honda’s customers receive high-quality products.
- Flexibility and scalability
HLNA’s distribution network is flexible and scalable to meet the changing needs of Honda’s business. The company can quickly adjust inventory levels and delivery schedules to accommodate fluctuations in demand.
- Cost-effectiveness
HLNA’s distribution network is designed to be cost-effective. The company uses a variety of strategies to minimize transportation and storage costs, such as consolidating shipments and using cross-docking techniques.
HLNA’s distribution network is a key component of the company’s success. The network allows HLNA to provide efficient, reliable, and cost-effective logistics services to Honda’s manufacturing and sales operations.
3. Transportation management
Transportation management is a critical component of Honda Logistics North America, Inc.’s (HLNA) operations. HLNA manages a network of transportation providers to ensure that parts and materials are delivered to Honda’s manufacturing plants and sales and marketing operations on time and in good condition. This is a complex task, as HLNA must coordinate with a variety of transportation providers, including trucking companies, railroads, and airlines. HLNA also must track the movement of shipments and ensure that they are delivered safely and securely.
HLNA’s transportation management system is a key competitive advantage for the company. By managing its own network of transportation providers, HLNA can reduce costs, improve efficiency, and ensure that shipments are delivered on time and in good condition. This helps Honda to meet its customer commitments and maintain its reputation for high quality products.
Here are some specific examples of how HLNA’s transportation management system benefits Honda:
- Reduced costs: HLNA’s transportation management system helps to reduce costs by consolidating shipments and negotiating favorable rates with transportation providers.
- Improved efficiency: HLNA’s transportation management system helps to improve efficiency by tracking the movement of shipments and identifying potential delays. This allows HLNA to take corrective action and ensure that shipments are delivered on time.
- Increased reliability: HLNA’s transportation management system helps to increase reliability by ensuring that shipments are delivered safely and securely. This helps Honda to avoid production disruptions and meet its customer commitments.
In conclusion, HLNA’s transportation management system is a key component of the company’s success. By managing its own network of transportation providers, HLNA can reduce costs, improve efficiency, and ensure that shipments are delivered on time and in good condition. This helps Honda to meet its customer commitments and maintain its reputation for high quality products.
4. Inventory control
Inventory control is a critical component of Honda Logistics North America, Inc.’s (HLNA) operations. HLNA implements robust inventory control systems to optimize stock levels and minimize waste. This is essential to HLNA’s ability to provide efficient and reliable logistics services to Honda’s manufacturing and sales operations.
HLNA’s inventory control systems track the movement of parts and materials throughout the supply chain. This allows HLNA to identify potential shortages and surpluses, and to take corrective action to ensure that the right parts are available at the right time and place. HLNA also uses inventory control systems to manage the flow of parts and materials through its distribution centers. This helps to minimize inventory levels and reduce storage costs.
HLNA’s inventory control systems are a key competitive advantage for the company. By optimizing stock levels and minimizing waste, HLNA can reduce costs, improve efficiency, and ensure that Honda has the parts and materials it needs to meet customer demand.
Here are some specific examples of how HLNA’s inventory control systems benefit Honda:
- Reduced costs: HLNA’s inventory control systems help to reduce costs by minimizing waste and optimizing stock levels. This helps Honda to avoid unnecessary inventory carrying costs and to free up cash flow for other purposes.
- Improved efficiency: HLNA’s inventory control systems help to improve efficiency by identifying potential shortages and surpluses, and by taking corrective action to ensure that the right parts are available at the right time and place. This helps Honda to avoid production disruptions and to meet customer demand.
- Increased customer satisfaction: HLNA’s inventory control systems help to increase customer satisfaction by ensuring that Honda has the parts and materials it needs to meet customer demand. This helps Honda to avoid backorders and to deliver products to customers on time.
In conclusion, HLNA’s inventory control systems are a key component of the company’s success. By optimizing stock levels and minimizing waste, HLNA can reduce costs, improve efficiency, and ensure that Honda has the parts and materials it needs to meet customer demand.
5. Customer service
Honda Logistics North America, Inc. (HLNA) is committed to providing exceptional customer service to both internal and external stakeholders. This commitment is essential to HLNA’s success, as it helps to build strong relationships with customers, suppliers, and employees. HLNA’s customer service team is dedicated to resolving issues quickly and efficiently, and to providing support and assistance to customers and suppliers. The team is also committed to continuous improvement, and is always looking for ways to improve the customer experience.
HLNA’s commitment to customer service is evident in a number of ways. For example, the company has a dedicated customer service team that is available 24/7 to answer questions and resolve issues. HLNA also has a number of customer service initiatives in place, such as a customer feedback program and a customer loyalty program. These initiatives help HLNA to track customer satisfaction and to identify areas for improvement.
HLNA’s commitment to customer service has a number of benefits for the company. First, it helps to build strong relationships with customers and suppliers. When customers know that they can rely on HLNA to provide excellent customer service, they are more likely to do business with the company. Second, HLNA’s commitment to customer service helps to reduce costs. By resolving issues quickly and efficiently, HLNA can avoid costly delays and disruptions. Third, HLNA’s commitment to customer service helps to improve employee morale. When employees know that they are supported by a strong customer service team, they are more likely to be productive and engaged.
In conclusion, HLNA’s commitment to customer service is essential to the company’s success. By providing exceptional customer service, HLNA builds strong relationships with customers and suppliers, reduces costs, and improves employee morale.
6. Cost efficiency
Honda Logistics North America, Inc. (HLNA) focuses on cost-effective solutions to minimize logistics expenses. This is a key component of the company’s success, as it allows HLNA to provide competitive pricing to its customers and to generate profits for Honda. HLNA achieves cost efficiency through a variety of measures, including:
- Consolidating shipments: HLNA consolidates shipments whenever possible to reduce transportation costs.
- Negotiating favorable rates with carriers: HLNA negotiates favorable rates with carriers to reduce transportation costs.
- Using cross-docking techniques: HLNA uses cross-docking techniques to reduce inventory carrying costs.
- Implementing lean manufacturing principles: HLNA implements lean manufacturing principles to reduce waste and improve efficiency.
HLNA’s focus on cost efficiency has a number of benefits for the company. First, it allows HLNA to provide competitive pricing to its customers. This helps HLNA to win new business and to retain existing customers. Second, HLNA’s focus on cost efficiency helps to generate profits for Honda. These profits can be used to invest in new equipment and technology, to expand the company’s operations, and to reward shareholders.
In conclusion, HLNA’s focus on cost efficiency is a key component of the company’s success. By focusing on cost efficiency, HLNA is able to provide competitive pricing to its customers, to generate profits for Honda, and to invest in the future.
7. Quality assurance
Quality assurance is a critical component of Honda Logistics North America, Inc.’s (HLNA) operations. HLNA maintains high standards of quality assurance throughout its operations to ensure that its customers receive high-quality products and services. This is essential to HLNA’s success, as it helps to build strong relationships with customers and to maintain Honda’s reputation for quality.
HLNA’s quality assurance program includes a number of measures to ensure that its products and services meet Honda’s high standards. For example, HLNA uses a variety of quality control techniques to inspect incoming parts and materials, and to monitor the production process. HLNA also has a dedicated team of quality assurance engineers who work to identify and resolve any potential quality issues.
HLNA’s commitment to quality assurance has a number of benefits for the company. First, it helps to build strong relationships with customers. When customers know that they can rely on HLNA to provide high-quality products and services, they are more likely to do business with the company. Second, HLNA’s commitment to quality assurance helps to maintain Honda’s reputation for quality. This reputation is essential to Honda’s success, as it helps the company to attract new customers and to retain existing customers.
In conclusion, HLNA’s commitment to quality assurance is essential to the company’s success. By maintaining high standards of quality assurance, HLNA builds strong relationships with customers, maintains Honda’s reputation for quality, and helps to ensure that Honda’s customers receive high-quality products and services.
8. Environmental sustainability
Honda Logistics North America, Inc. (HLNA) prioritizes environmental sustainability in its logistics practices as a key component of its commitment to corporate social responsibility. Recognizing the impact of logistics operations on the environment, HLNA actively implements sustainable practices to minimize its ecological footprint and contribute to a greener supply chain.
HLNA’s environmental sustainability efforts are evident in several key areas:
- Fuel-efficient transportation: HLNA optimizes transportation routes and leverages fuel-efficient vehicles to reduce carbon emissions.
- Modal shift: The company explores alternative modes of transportation, such as rail and intermodal shipping, to minimize the environmental impact of long-haul trucking.
- Sustainable packaging: HLNA promotes the use of eco-friendly packaging materials and minimizes waste through reusable packaging solutions.
- Waste reduction and recycling: The company implements waste management programs to reduce, reuse, and recycle materials generated in its distribution centers and transportation operations.
By prioritizing environmental sustainability, HLNA aligns with Honda’s global commitment to environmental stewardship. The company’s sustainable logistics practices not only reduce its environmental impact but also contribute to a broader movement towards a more sustainable and resilient supply chain.
In conclusion, HLNA’s focus on environmental sustainability underscores the company’s commitment to responsible business practices. Through its eco-conscious initiatives, HLNA demonstrates a proactive approach to mitigating its environmental footprint and contributing to a more sustainable future for the logistics industry.
9. Technology adoption
Technology adoption is a key component of Honda Logistics North America, Inc.’s (HLNA) operations. HLNA leverages advanced technologies to enhance efficiency and accuracy throughout its logistics processes, contributing significantly to the company’s overall success.
One of the most important ways that HLNA uses technology is to optimize its transportation and distribution networks. The company uses a variety of software applications to track shipments, identify potential delays, and find the most efficient routes. This helps HLNA to reduce transportation costs and improve delivery times.
HLNA also uses technology to automate many of its warehouse and distribution center operations. This includes using automated guided vehicles (AGVs) to move materials around the warehouse, and using RFID tags to track inventory levels. This automation helps HLNA to improve efficiency and accuracy, and to reduce labor costs.In addition to using technology to optimize its operations, HLNA also uses technology to improve customer service. The company has a web-based portal that allows customers to track their shipments and access other information about their orders. HLNA also uses social media to communicate with customers and to provide support.HLNA’s adoption of technology has had a major impact on the company’s success. By using technology to improve efficiency and accuracy, HLNA has been able to reduce costs, improve customer service, and gain a competitive advantage in the logistics industry.
Frequently Asked Questions about Honda Logistics North America, Inc.
This FAQ section aims to provide concise and informative answers to common inquiries regarding Honda Logistics North America, Inc. (HLNA).
Question 1: What is the primary function of Honda Logistics North America, Inc.?
Answer: HLNA serves as Honda’s primary logistics provider in North America, managing the efficient flow of parts and materials to Honda’s manufacturing plants and sales operations.
Question 2: How does HLNA contribute to Honda’s overall success?
Answer: HLNA’s expertise in logistics management ensures a seamless supply chain for Honda’s manufacturing operations, reducing production disruptions and enabling timely delivery of products to customers.
Question 3: What are the key aspects of HLNA’s distribution network?
Answer: HLNA operates a vast network of distribution centers strategically located to optimize inventory management, ensure quality control, and adapt to changing demand.
Question 4: How does HLNA manage transportation for Honda’s logistics operations?
Answer: HLNA manages a network of transportation providers, leveraging technology to track shipments and identify potential delays, resulting in efficient and reliable delivery of goods.
Question 5: What measures does HLNA take to ensure customer satisfaction?
Answer: HLNA is dedicated to providing exceptional customer service, with a focus on resolving issues promptly, offering support, and implementing continuous improvement initiatives to enhance the customer experience.
Question 6: How does HLNA prioritize sustainability in its operations?
Answer: HLNA actively promotes environmental sustainability, adopting fuel-efficient transportation, exploring alternative modes, implementing waste reduction programs, and utilizing eco-friendly packaging materials.
Summary: HLNA plays a crucial role in Honda’s North American operations, leveraging its expertise in logistics management, advanced technologies, and commitment to sustainability to ensure efficient and reliable delivery of parts and materials, contributing to Honda’s overall success and customer satisfaction.
Transition: For further insights into Honda Logistics North America, Inc., explore the following sections covering various aspects of the company’s operations and achievements.
Tips by Honda Logistics North America, Inc.
Honda Logistics North America, Inc. (HLNA) offers valuable insights and recommendations to enhance logistics efficiency and effectiveness. Here are some tips from HLNA:
Tip 1: Optimize Transportation Routes
HLNA leverages advanced route optimization software to determine the most efficient transportation routes, reducing fuel consumption, emissions, and delivery times. By considering factors such as traffic patterns, weather conditions, and vehicle capacity, HLNA ensures optimal utilization of resources.
Tip 2: Implement a Robust Inventory Management System
HLNA emphasizes the importance of a robust inventory management system to maintain optimal stock levels, minimize waste, and enhance supply chain visibility. By utilizing real-time inventory tracking and forecasting tools, businesses can prevent shortages, reduce storage costs, and improve overall inventory accuracy.
Tip 3: Leverage Technology for Automation
HLNA advocates for the adoption of automation technologies to streamline logistics processes and improve efficiency. Automated guided vehicles (AGVs) and RFID tags can enhance warehouse operations, reduce manual labor, and minimize errors, leading to increased productivity and cost savings.
Tip 4: Prioritize Environmental Sustainability
HLNA promotes environmentally sustainable practices throughout its operations, including utilizing fuel-efficient vehicles, exploring alternative modes of transportation, and implementing waste reduction programs. By adopting sustainable initiatives, businesses can reduce their carbon footprint, comply with environmental regulations, and enhance their corporate social responsibility.
Tip 5: Foster a Collaborative Supplier Relationship
HLNA emphasizes the significance of fostering collaborative relationships with suppliers. Open communication, regular performance evaluations, and joint problem-solving can strengthen the supply chain, improve delivery reliability, and reduce potential disruptions.
Summary: By incorporating these tips from Honda Logistics North America, Inc., businesses can enhance their logistics operations, optimize resource utilization, and gain a competitive advantage in the market. Embracing technological advancements, prioritizing sustainability, and fostering supplier collaboration are key to driving efficiency, reducing costs, and achieving operational excellence in the logistics industry.
Transition: To delve deeper into the world of logistics and supply chain management, explore the following sections for insightful articles, case studies, and industry best practices.
Conclusion
Honda Logistics North America, Inc. (HLNA) plays a pivotal role in Honda’s North American operations, providing comprehensive logistics services that ensure the efficient and reliable flow of parts and materials to Honda’s manufacturing plants and sales operations. HLNA’s commitment to quality, cost-effectiveness, and environmental sustainability has positioned the company as a leader in the logistics industry.
HLNA’s expertise in transportation management, inventory control, and customer service has enabled Honda to minimize production disruptions, meet customer demand, and maintain its reputation for high-quality products. The company’s focus on technology adoption and process optimization has further enhanced its efficiency and accuracy. By prioritizing environmental sustainability, HLNA aligns with Honda’s global commitment to corporate social responsibility and contributes to a greener supply chain.
As the logistics industry continues to evolve, HLNA is well-positioned to adapt and thrive. The company’s commitment to innovation, collaboration, and continuous improvement will undoubtedly continue to drive its success and contribute to Honda’s overall competitiveness.